UPSTREAM OIL & GAS PROCESS ENGINEERING SERVICES
Although the individual processes are not as complicated as refinery processes, the dynamic and shutdown / startup issues are complex, especially in remote locations. A thorough understanding of these issues for startup and shutdown, manned and unmanned facilities, emergency control and overpressure protection, black startups, compressor train balancing and many other issues are provided by our team.
PROCESS is able to provide a number of standard oil and gas engineering services to upstream processors for both Onshore facilities as well as Offshore.
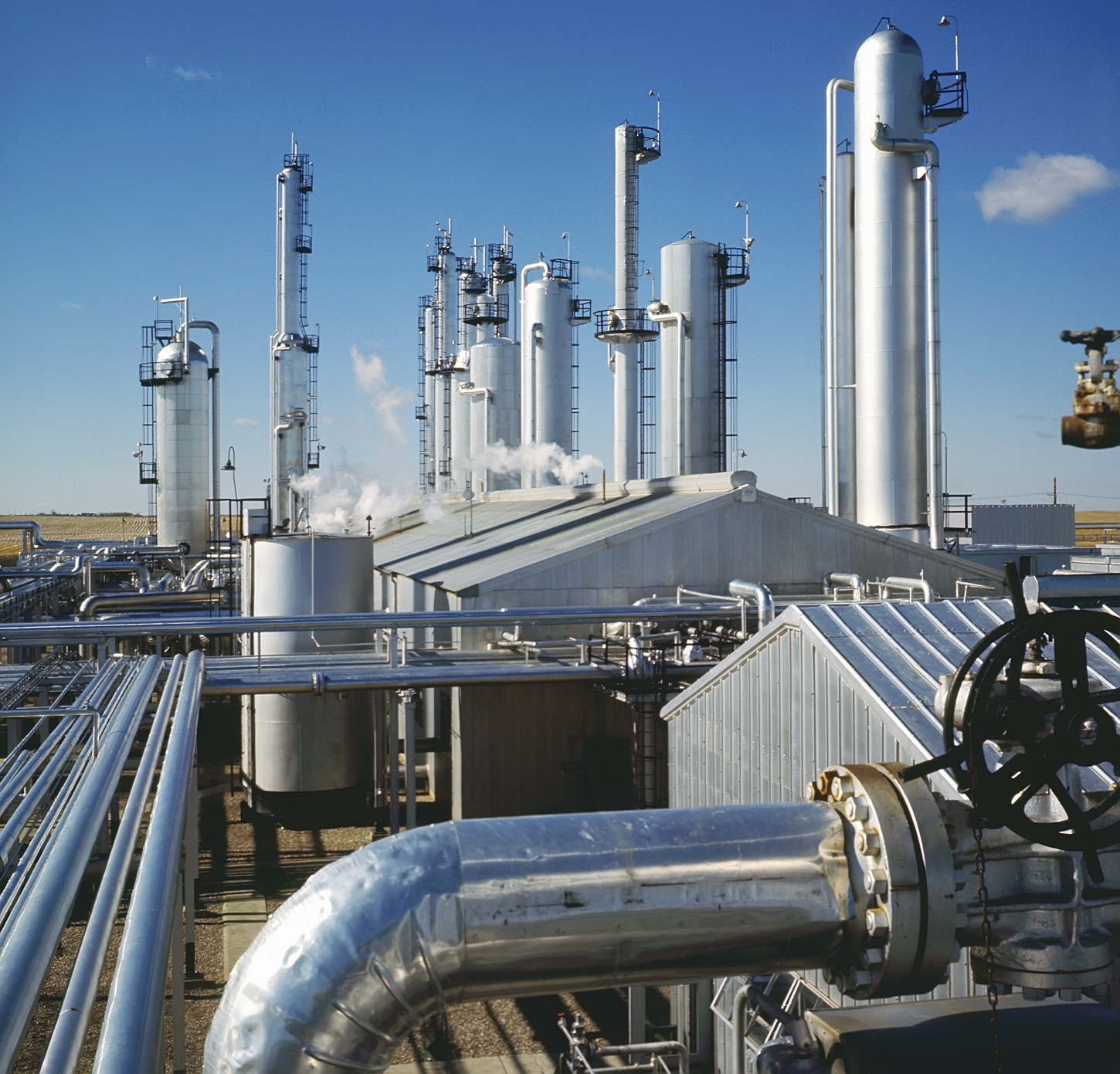
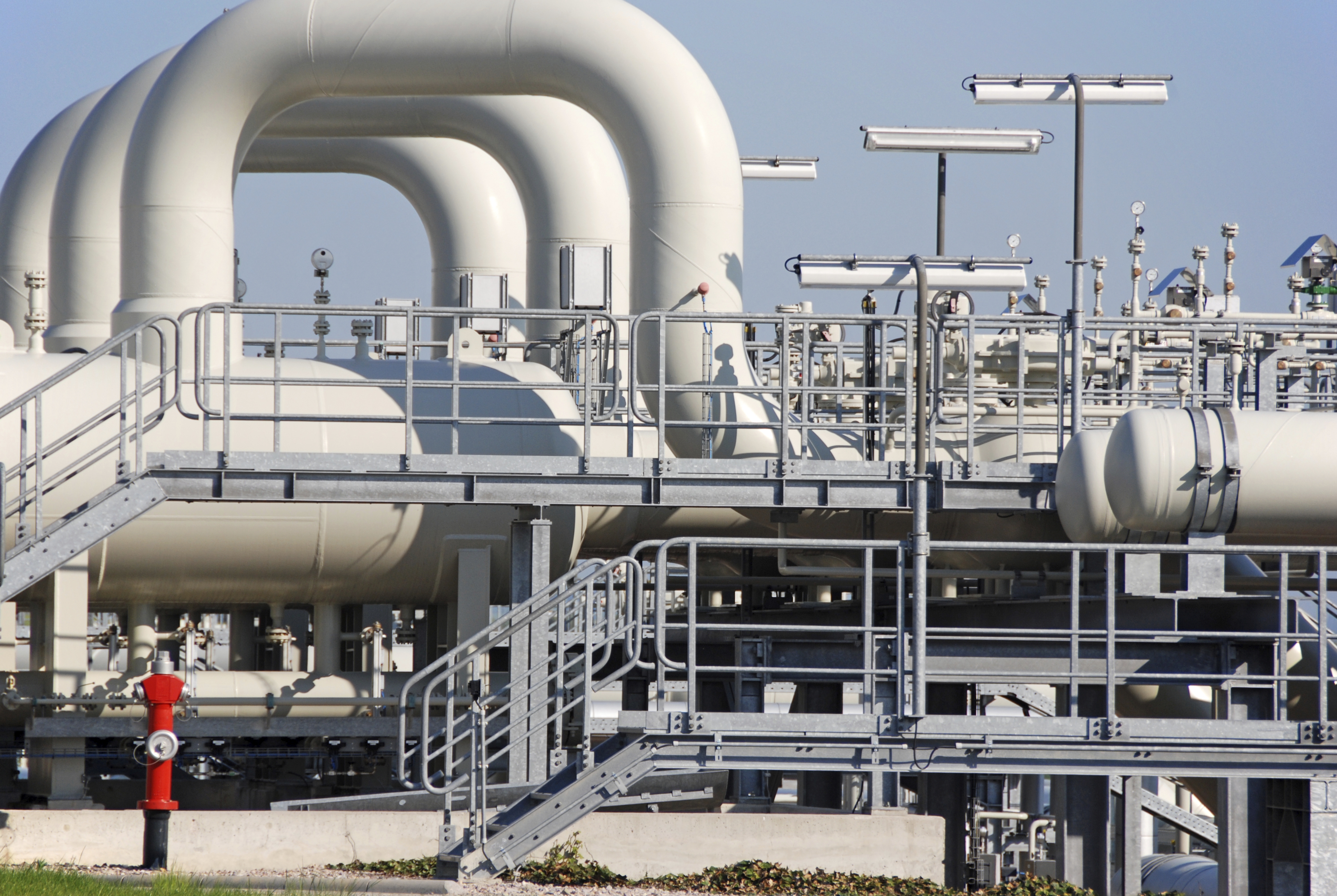
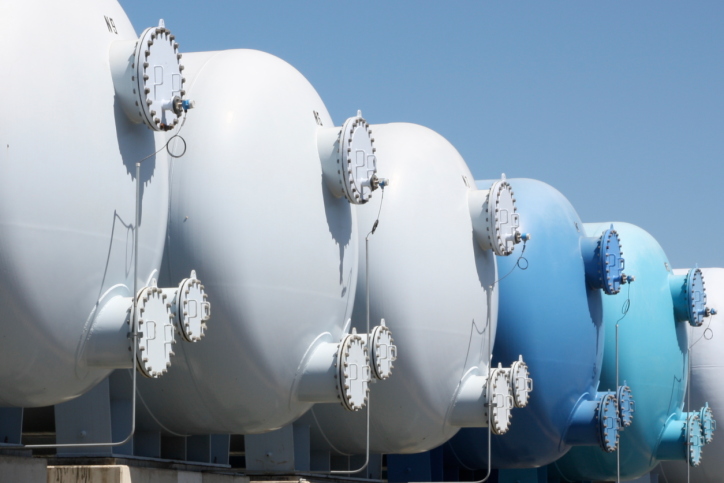
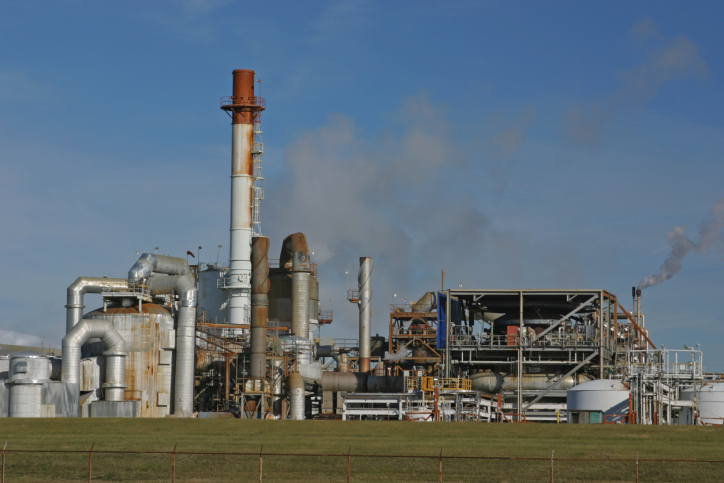
PROCESS can help with the following common issues in all areas of upstream processing.
Upstream Oil Processing
- Oil/Gas Separation and Testing Separation
- Flaring reduction/elimination
- Hydrate prediction and prevention
- MEG/Corrosion Inhibitor Injection
- Glycol dehydration
- Desanding
- Desalting
Gas Processing
- Slugcatcher specification
- Hydrate prediction and prevention
- Dehydration: MEG injection, silica gel, zeolite adsorption
- Amine absorption
- Dewpoint control unit
- Mercury removal unit
- Gas pipeline compression
- Flow metering
- Condensate stabilization
NGL processing and LPG Fractionation
- Merox treatment
- Benzene extraction
- Advanced column control
- Condensate stabilization
- iC5 rich extraction
PETROLEUM REFINING
PROCESS provides a wide range of oil and gas engineering services to petroleum refineries. Our company has a great deal of refinery unit design, process safety, operations, and troubleshooting experience. After proving ourselves on smaller sized projects, many of our clients begin utilizing our services on a routine basis as an extension of their own in-house engineering team. From solving a vapor-locked pump problem to designing complete units, PROCESS can meet your needs.
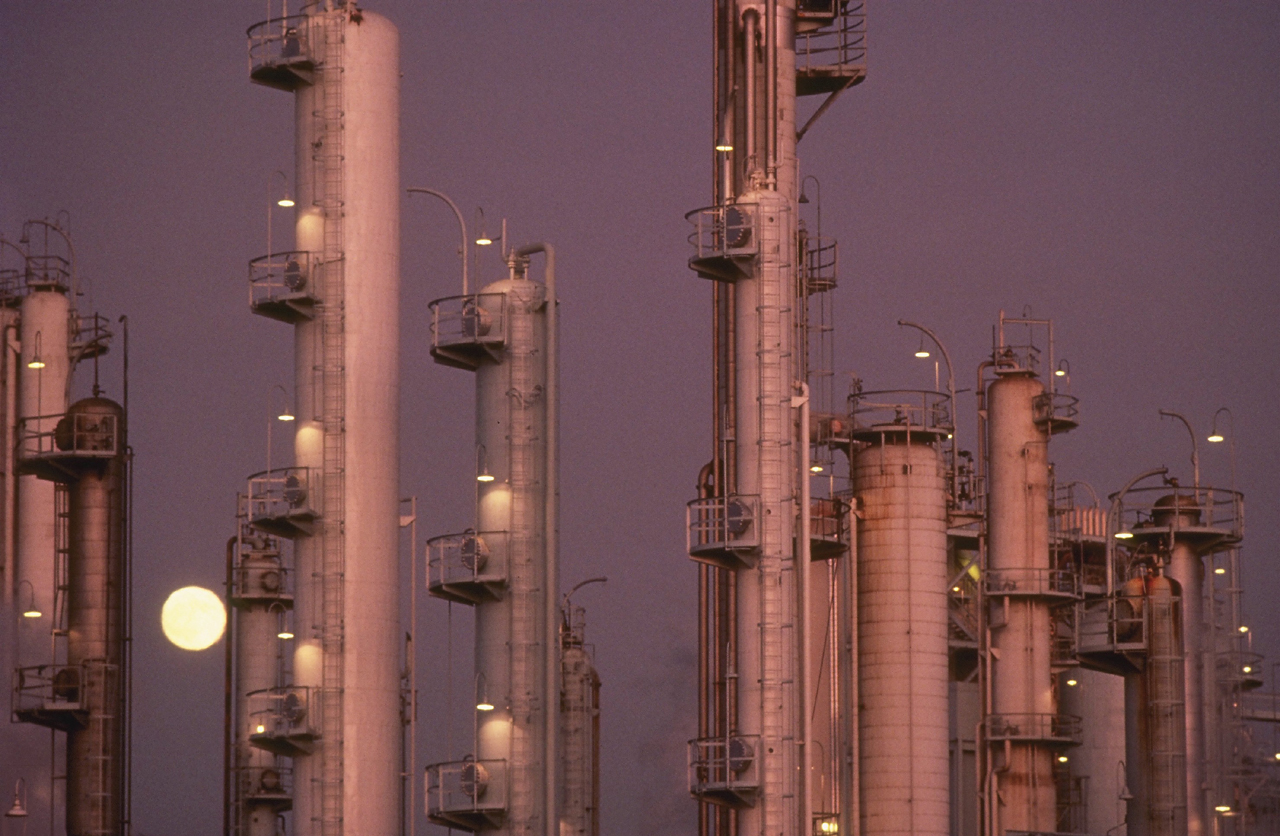
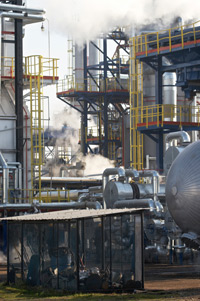
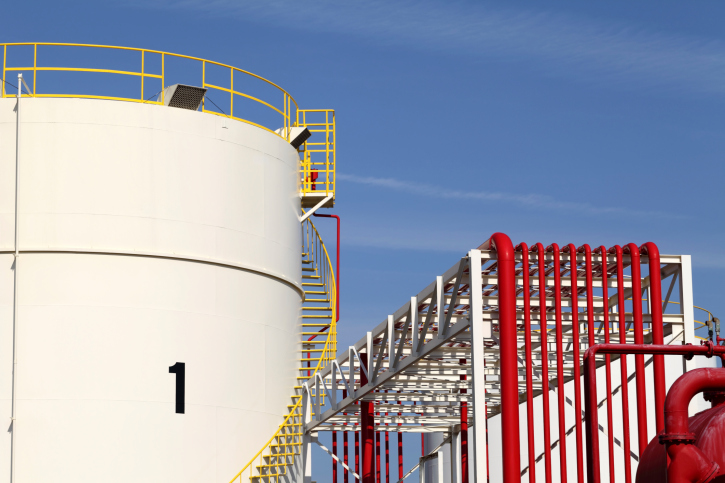
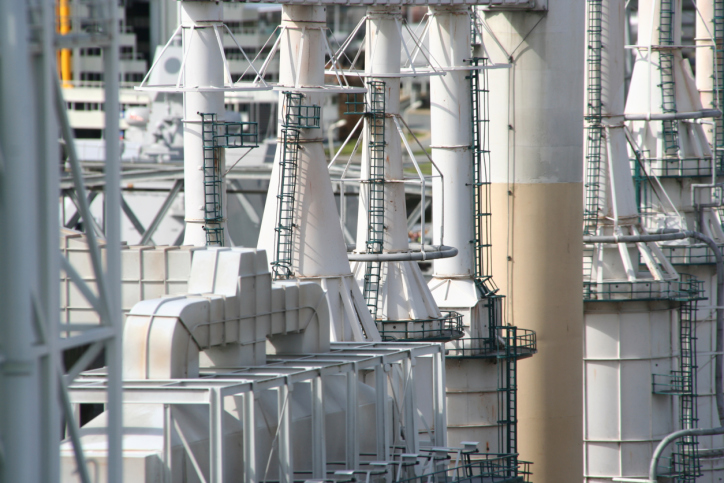
Our Refining Niche
PROCESS can provide preliminary design packages, Heat & Mass Balances, process and equipment design packages, and any number of front-end related services. This is true for most typical refinery processes, a few of which include:
- Crude Units
- Vacuum Distillation Units
- Hydrotreating
- Isomerization
- Fluid Catalytic Cracking
- Reforming
- Coking
- and more….
We have worked on a broad base of refinery projects for many years, and that breadth allows us to rapidly respond to our clients’ needs with quality information and reliable front-end design packages. A few of the project types completed by PROCESS have included:
- Capacity Evaluations
- Unit Debottlenecking
- Fractionation Upgrade Design
- Capital Project Development Support (FEL-0, 1, 2, 3)
- Unit Simulation and Modeling
- Energy Usage Improvements
- Flare Header Studies
- Relief Valve Sizing Validation
- Balance of Process Design for New Technology Deployment
- and more….
PROCESS is also able to provide a qualified 3rd party evaluation of refinery unit design packages and we are very adept at conducting unit capacity evaluations and revamp studies, utility evaluations, small to medium sized process designs, relief valve studies, and almost any refinery process safety related function.
PROCESS can also provide expert consulting oil and gas engineering services and bid evaluations on larger projects that may require additional resources. Examples of such larger projects would include reviewing the design package for a new Fluid Catalytic Cracker (FCC) unit or Hydrocracker.
A Great Fit for All Sizes of Refiners
PROCESS is uniquely structured for providing services to small to medium sized refineries (10,000 BBL/day to 200,000 BBL/day) in addition to larger refineries. Even a small refiner should expect a premier level of service, and that’s what PROCESS provides. In today’s world even the smallest of refineries has to boost yields, increase utilization, and minimize operating costs or they may not be able to effectively compete as an independent refiner.
One specific example of how smaller refineries can benefit from our oil and gas process engineering services is by having us provide the process design work necessary to implement the technologies most suited for smaller sized refineries such as the Dupont Isotherming process. PROCESS can first help the client identify and evaluate such technologies and then provide the ‘balance of plant’ process design to effectively integrate the new technology into a refiner’s existing operations. This often includes modifications to the existing refinery utilities systems and adaptations to the technology package that take into account specific conditions at a particular location. Utilizing PROCESS for this purpose helps ensure an effective startup and minimizes refinery down time.
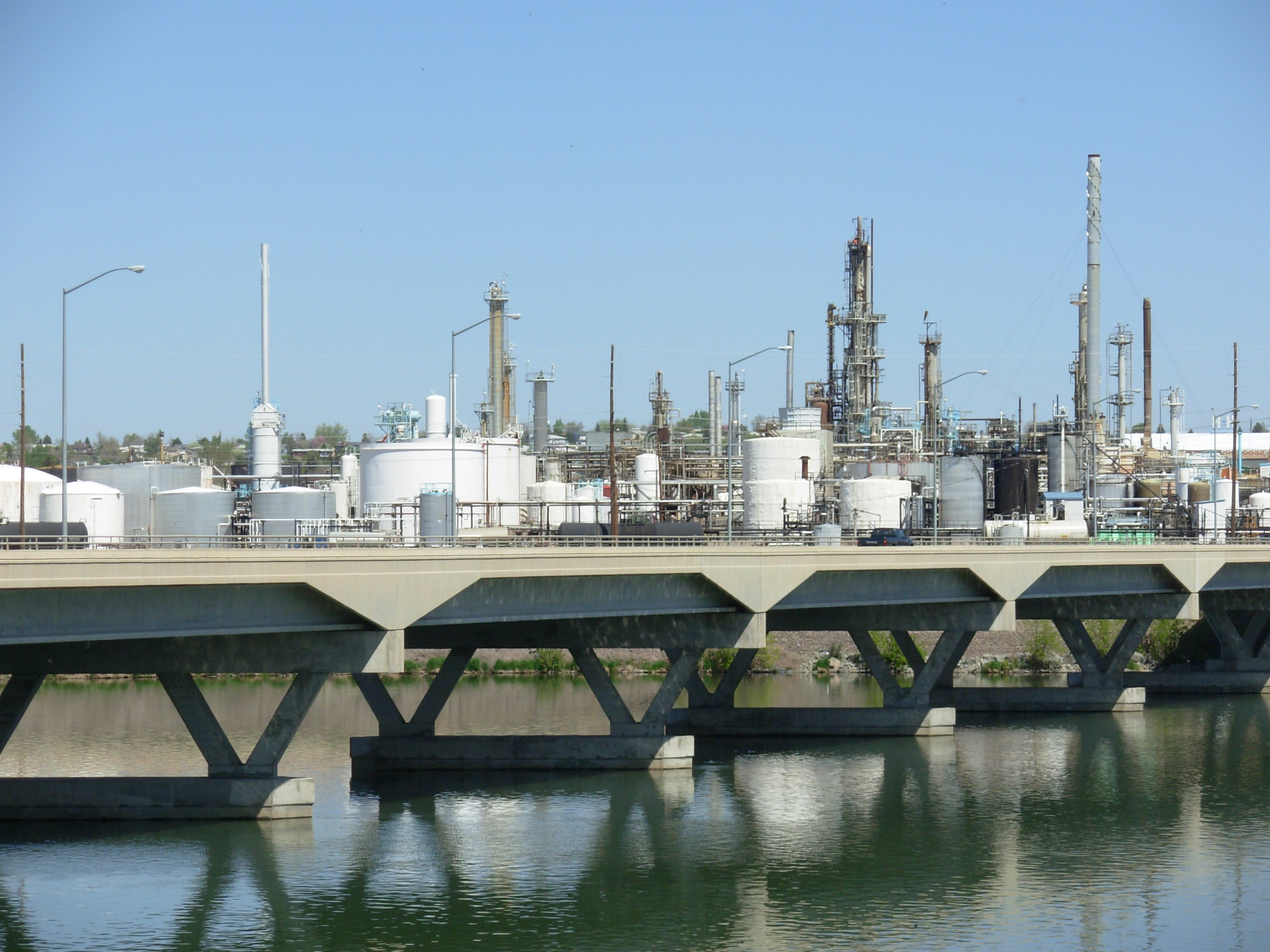
LICENSED OIL AND GAS PROCESS TECHNOLOGY
Integrating Licensed Technologies
PROCESS can first help the client identify and evaluate technologies suitable for their well composition and then provide the ‘balance of plant’ process design to effectively integrate the new technology into a client’s onshore or offshore platform operations. The process work is not finished after a technology is purchased, there is almost always a host of plant integration issues outside the battery limits. This often includes utilities systems, pretreatment adaptations for specific feeds, downstream storage, and more. Utilizing PROCESS for this purpose helps ensure an effective rollout will occur, and helps remove liability for both the client and the technology provider.
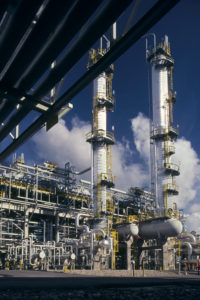
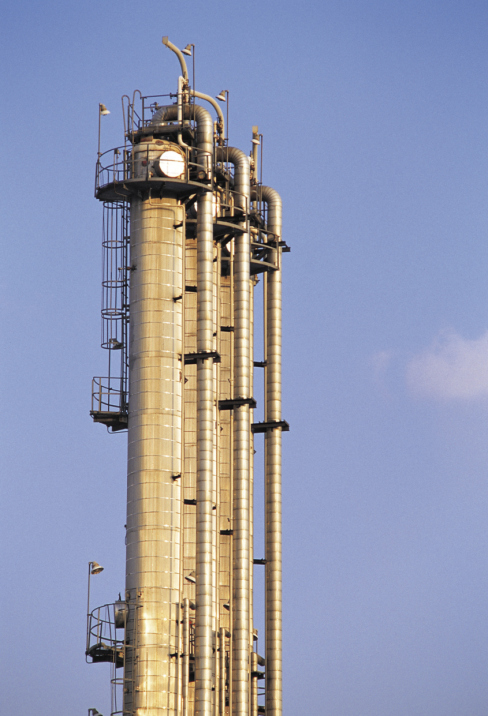
Taking Advantage of Gas To Liquids Opportunities
With today’s demand for liquid fuels, gas well operators are more and more looking toward Gas To Liquids (GTL) technologies as a way to convert stranded gas or gas that was once flared to a substantial salable product such as kerosene or jet fuel. The opportunities for enhanced profitability is especially good for remote fields with large gas content. In fact, most of the major unit operations are contained within a few purchased process technologies such as Rectisol® and Selexol® which remove acid gases such as H2S, CO2, etc. We have significant experience in Gas to Liquids (GTL) processes and can provide valuable assistance in implementing such new processes. Whether the process is making gasoline, diesel, or simply cleaning up and liquefying raw gas to meet LNG specifications, PROCESS can help.
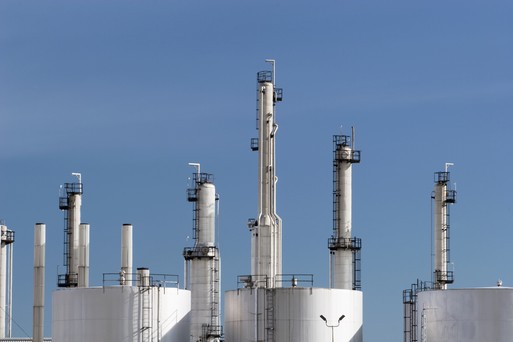
Taking Advantage of Gas To Liquids Opportunities
Amine Absorption
PROCESS’ engineers have in-depth experience with amine processing, including conversion of plant equipment and processing from one amine to BASF’s MDEA, as well as plant specification and troubleshooting. This experience also includes crucial equipment differences caused by increased loading of the amine.
PROCESS is able to optimize amine losses and energy consumption, sometimes by installing advanced control schemes.
LNG LIQUEFACTION and REGASIFICATION
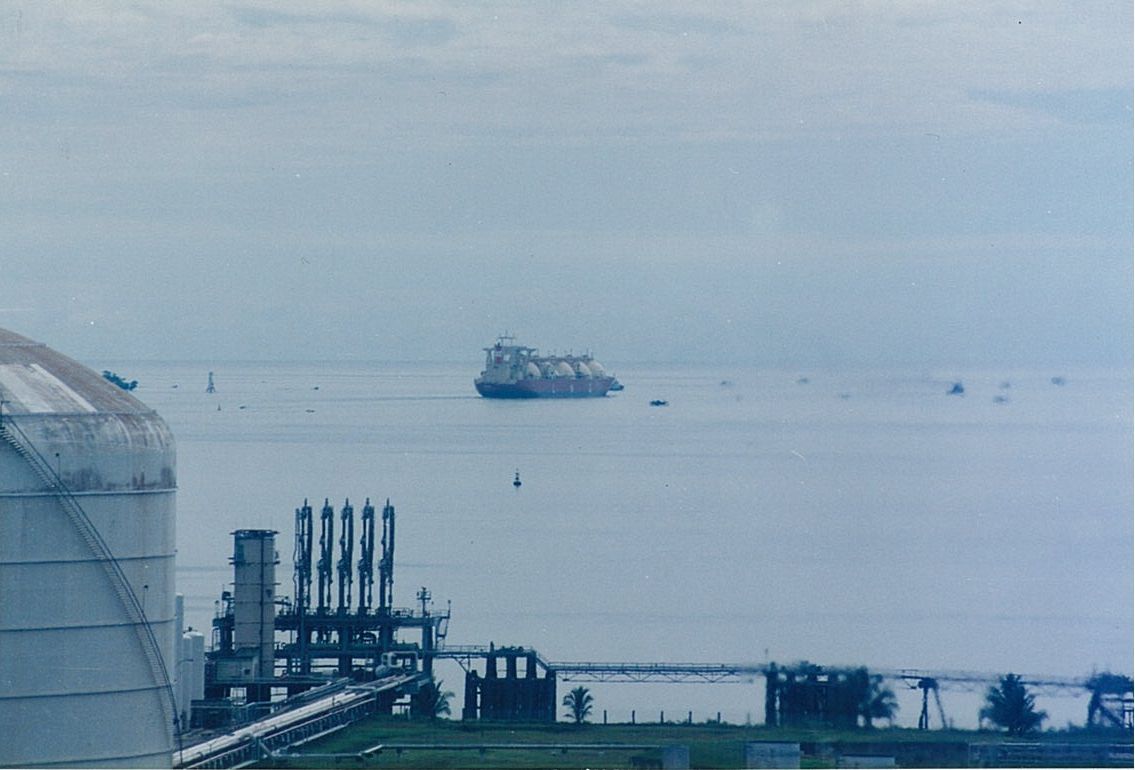
Specialized LNG Experience
When it comes to regasification terminals, we are able to perform an equipment layout and rough cost estimate as part of a conceptual design package. A conceptual process design would include key features such as BOG (boil-off gas) suppression, reloading capability (if required), firewater minimization, electrical usage minimization, and tank sizing, in addition to any other process features required by the client.
Liquefaction installations are unique facilities and PROCESS is able to perform commissioning support, troubleshooting, and debottlenecking, as well as many design and operations support tasks.
For LNG receiving terminals PROCESS is able to provide items such as: major equipment lists, layout and cost estimates with semi-detailed unit costs and assembly level line items.
PROCESS is familiar with the following additional aspects of industrial process projects:
Procedures
Documentation
Layouts
Cost estimates
Design standards
Hazards identification (HAZOP)
Process safety program support (PSM and RMP)
Electrical/civil/mechanical/process/piping interfacing
Vendor interface
Cause & effects
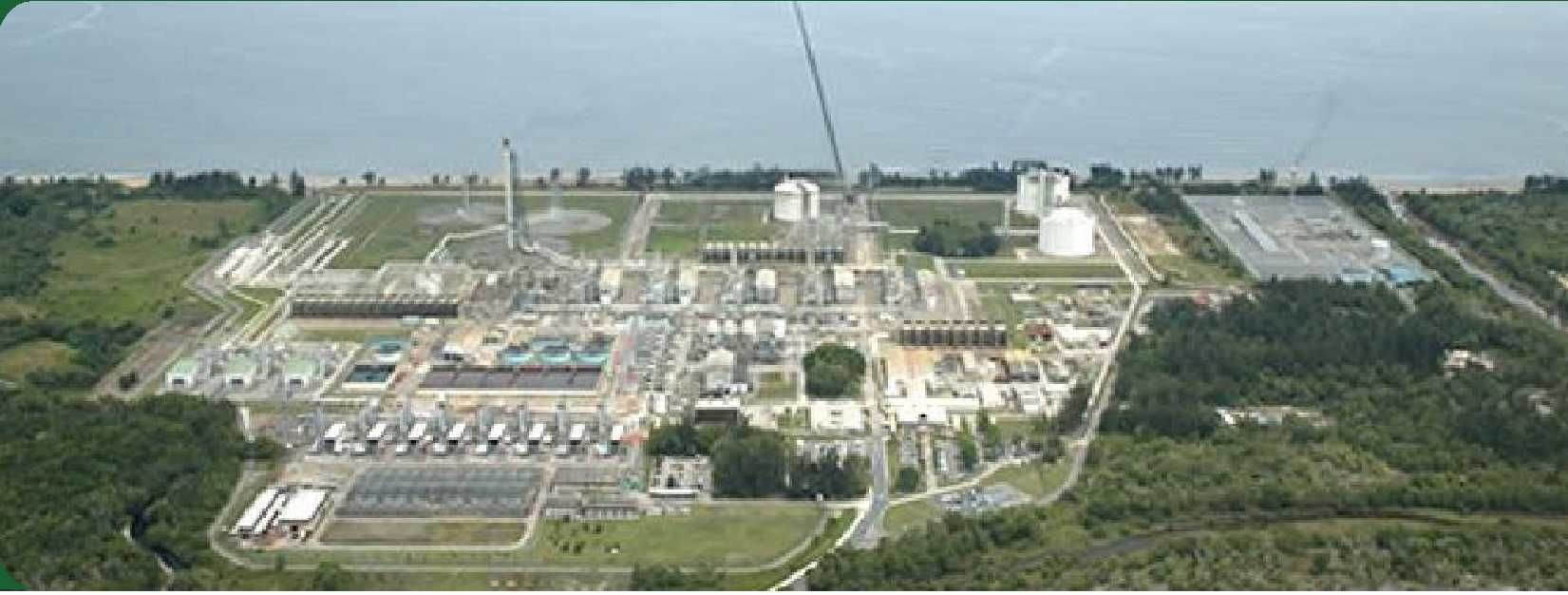
What We Offer
In addition to specialty areas of expertise, all of our standard services and deliverables apply equally as well to LNG facilities of all types. These include:
- Conceptual process design development
- Capital Project Development Support (FEL-1, 2, 3)
- Front End Engineering Design packages (FEED) and FEED verification
- Preliminary and final process design packages (basic engineering / schedule A / etc.)
- Technical and economic process alternatives evaluations and feasibility studies
- Design calculations and technical reporting
- Process simulations and modeling
- Mass and energy balances
- Unit operation design/evaluation
- Debottlenecking studies
- Piping system hydraulics calculations
- Process control scheme development
- Control system startup, tuning, optimization
- Creating Process Flow Diagrams (PFDs), Piping and Instrumentation Diagrams (P&IDs), and Process Control Diagrams (PCDs)
- Process/equipment bid package preparation
- Equipment specifications, and vendor technical / cost proposal evaluation and recommendations
- Detail design and construction phase process oversight and support
- Commissioning and startup support
- Process evaluation, troubleshooting and optimization
- Conducting Process Hazard Analyses (PHAs) and developing risk management plans
- Independent 3rd party design review
- On-site process modification/construction oversight
- Commissioning and startup
- Troubleshooting and optimization
- Development of operating procedures
- Development of process documentation
LNG Systems Experience
LNG facilities utilize a number of challenging compression and refrigeration systems. Dynamic simulation (dynamic compression evaluation programs) help ensure systems are protected and adequately designed for frequent start up and shut down under a variety of load conditions. Here are some examples of common LNG subsystems:
Process Systems
-
- Wellheads
- Pipelines
- Slugcatchers
- Condensate separation
- Benzene removal
- CO2CO2 Absorption
- Driers
- Mercury absorption
- Pre-cooling
- Heavy hydrocarbon columns
- Liquefaction
- Sub-cooling
- N2N2 removal
- CO2CO2 liquefaction/re-injection
- LNG storage/loading
- LPG fractionation/storage
- Refrigerant makeup
- Utility systems
- Mono-Ethylene Glycol (MEG)
- Gas turbines and electrical (plus emergency power)
- Flares and blowdown
- Compressed air
- Steam
- Tempered water
- Cooling water
- Hot oil
- Nitrogen production
- Liquid Nitrogen storage
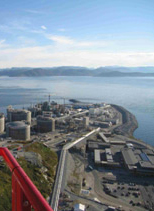
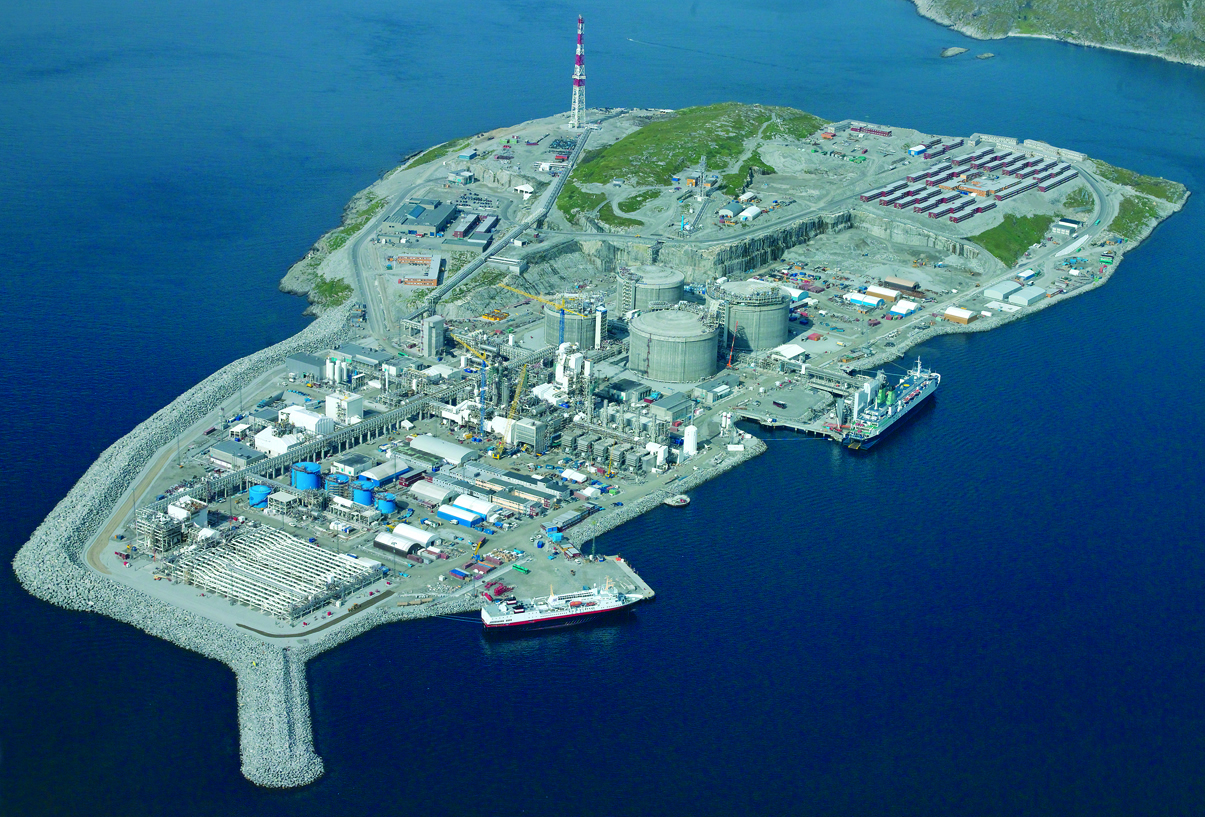
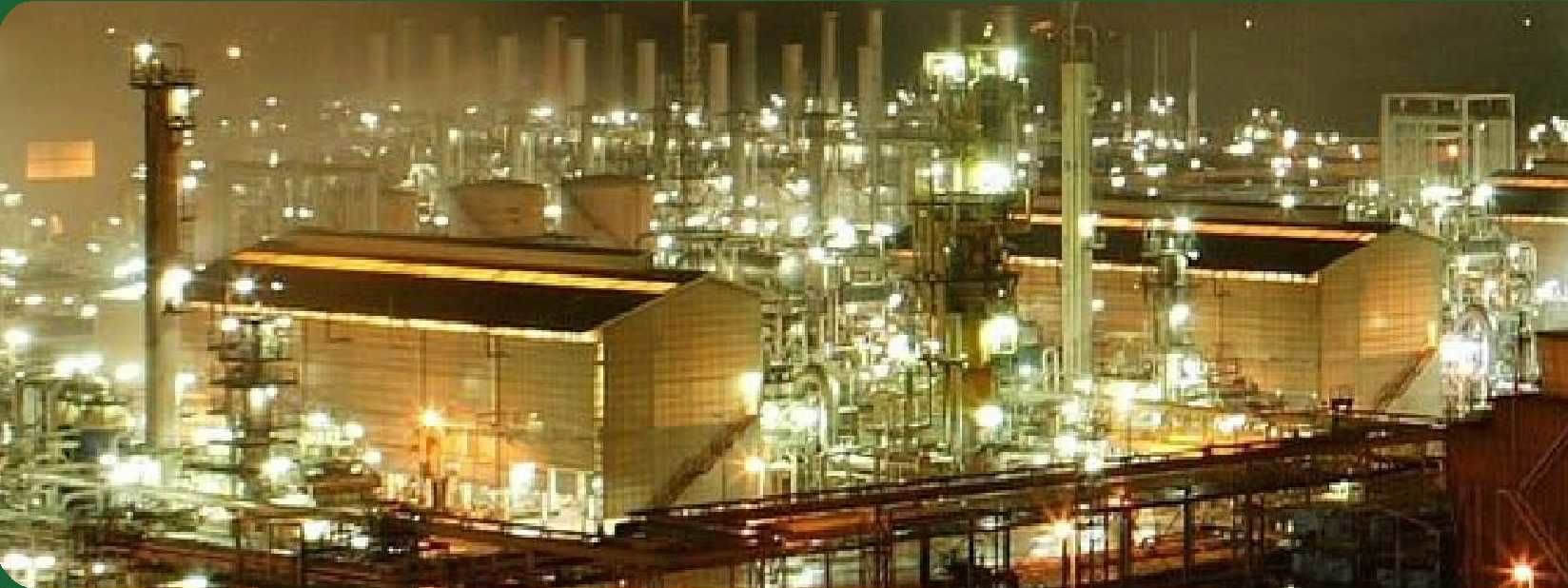
Taking Advantage of LNG Opportunities
With today’s demand for clean burning, easily transportable fuels, LNG is rapidly becoming a fuel of choice for many applications. In this environment, plant operators and their engineering/construction partners must be able to design robust facilities accurately and efficiently. PROCESS has over 50 process engineers ready to assist by providing process chemical engineering expertise throughout the course of your next project.
OFFSHORE
Our Experience
Our company and our engineers have a great deal of process design, operations, and process safety experience within many types of oil, gas, and refining operations. While our direct offshore experience is limited, the fundamentals of processing materials onshore or offshore is the same, however, just like many other markets, offshore processes have their own set of special considerations (safety features, space constraints, weight issues, etc.). Because our company is only focused on chemical process engineering, our process engineers work in a wide variety of markets and processes, each having its own set of special requirements that a design engineer must consider and conform to. This adaptability means we can easily pick up on the particular requirements of any given platform operation or Floating Production, Storage, and Offloading facilities (an FPSOs) and provide process design services that get the job done and comply with these requirements.
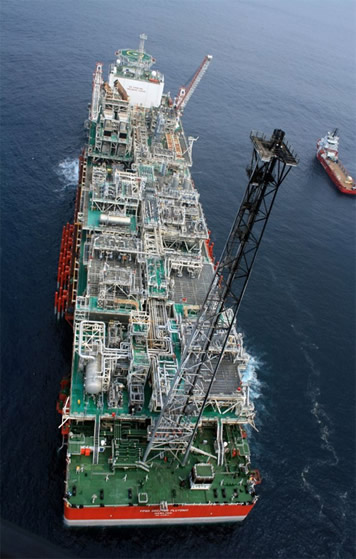
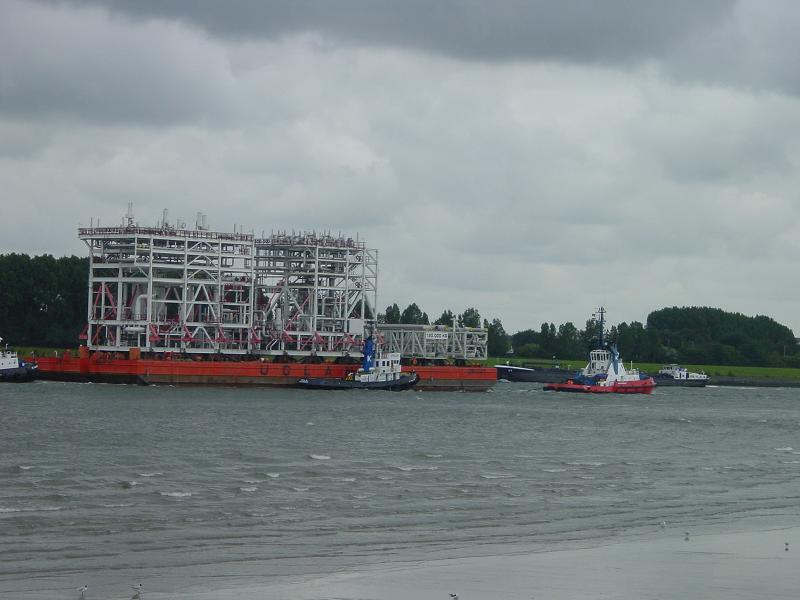
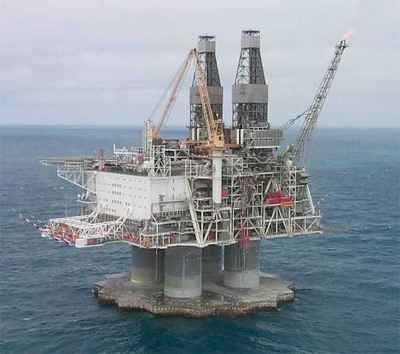
Our Services
PROCESS can provide a large number of front-end process design and process safety services to offshore operations. These services include:
- Feasibility studies
- Capital Project Development Support (FEL-0, 1, 2, 3)
- Conceptual/preliminary front end engineering design packages (FEED)
- FEED verification services
- Mass and energy balances
- Process simulation and hydraulics modeling
- Process design packages with equipment specifications
- Process Hazard Analyses (PHAs)
- Safety Integrity Level (SIL) selection analyses for Safety Instrumented Systems (SISs)
- Layer of Protection Analysis (LOPA)
- Compliance Audits
- Hazard assessments (including HAZOPs)
- Resolving/implementing PHA recommendations
- Developing PSM/RMP programs
- Developing process safety information
- PHA facilitation training
These services can be applicable to FPSOs or topside platform processing. Typical operations include gas compression, oil/gas dehydration, flaring systems, and other topside separations/cleanup processes.