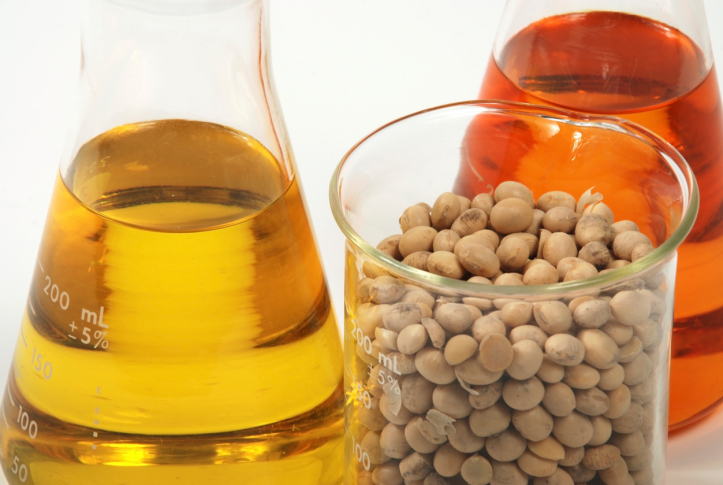
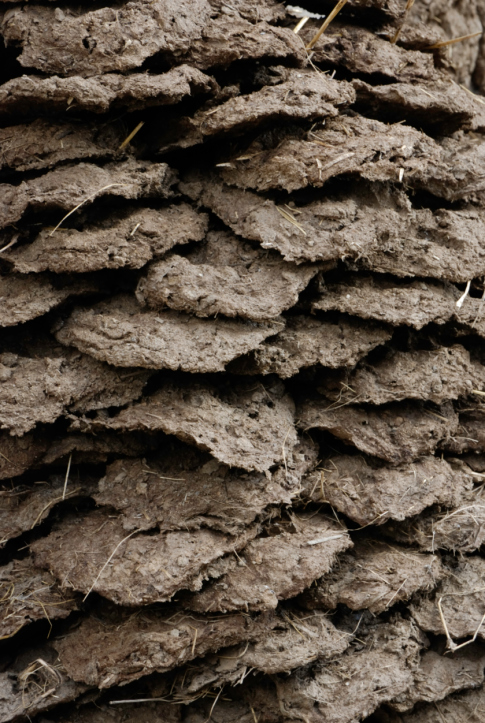
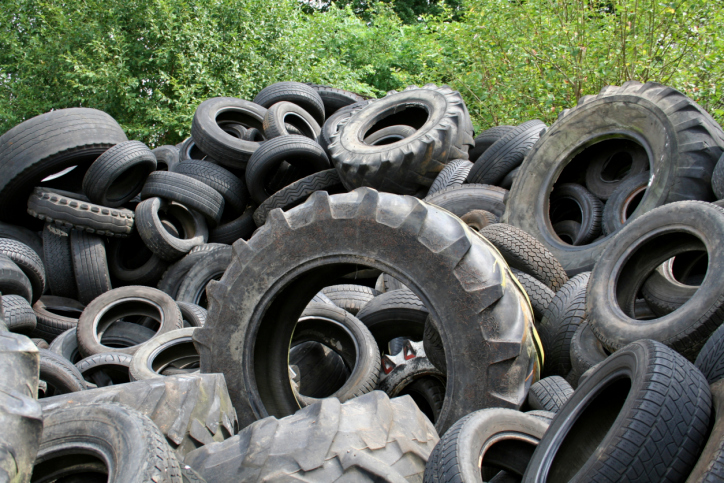
A New Frontier in Process Development
Developments and process proposals within the recently-emerged “Alternative Fuels Industry” are truly staggering. While everyone seems to have a great idea, both technical and economic realities will slowly but surely eliminate those processes which are not technically viable or economically attractive. Depending on the feedstocks, the conversion processes may include fermentation, chemical extraction, steam stripping, azeotropic distillation, gasification, or simply hydrotreating. The design, scale-up, or refinement of such processes are all areas where PROCESS’ experienced process design engineers can provide alternative energy and chemical solutions. We have significant experience in Gas to Liquids (GTL), Ethanol process engineering and design, and Biodiesel production processes on both a pilot and commercial scale.
Technical Areas to Consider
If gasification technology is being used, has this technology been adequately developed or purchased from a proven source? Can it be practiced economically at the client’s scale? How will the gasifier be fed from a material handling standpoint? Have realistic and efficient gas cleaning and heat recovery systems been developed?
Our experience has been that one of the most difficult and underestimated stages of many gasification processes is the gas cleanup of the product streams exiting the gasifier or pyrolysis unit. Many components can exist which can be problematic even at relatively low concentration levels. PROCESS has the experience and knowledge to recommend the most effective, reliable, and cost-efficient treatment options and alternative energy solutions for such streams. The same process benefits apply when dealing with the highly energy-intensive dehydration processes involved in the production of many liquid fuel products via fermentation.
New Technology Feasibility Determination
In cases where a new process concept is contemplated, a critical engineering validation is needed to determine if further effort and funding are justified. The sooner that the process can be economically validated and justified, the better it is for everyone involved. Partial lab or pilot scale data may exist, but rarely have all the critical factors been evaluated in the systematic manner which is needed to move forward with confidence. PROCESS can work with such infant processes to make sure the process concept is grounded in fundamental laws of thermodynamics, chemistry, mass transfer, etc. and not on ‘smoke & mirrors’ or wishful thinking. We will pick the process apart, ask the hard questions, and maybe even recommend that it be sent back to the drawing board. However, once PROCESS is satisfied that the critical issues have been addressed in an effective manner, the client will have the supporting data and documentation needed to confidently move forward with the economic evaluation. PROCESS can also assist here by using our knowledge and process simulation tools to accurately predict yields, product quality, and other variables for different operating scenarios or feed stocks. New technology groups will find investors much more receptive when the technical due diligence has been thoroughly performed in advance.
Existing Process Scale-Up
In cases where clients have already performed the necessary preliminary engineering and laboratory / bench-scale testing, PROCESS can facilitate a design basis formulation followed by the pilot-plant design and test protocol. We can even assist in the technical oversight of the pilot-plant trials if needed. PROCESS can further assist in the evaluation of the data and provide the scale-up design to a demonstration or commercial-sized process. Here more than anywhere, our engineering staff’s extensive plant operations experience can be put to profitable use by the client to identify and address potential operability issues that might otherwise plague the operation for years to come.
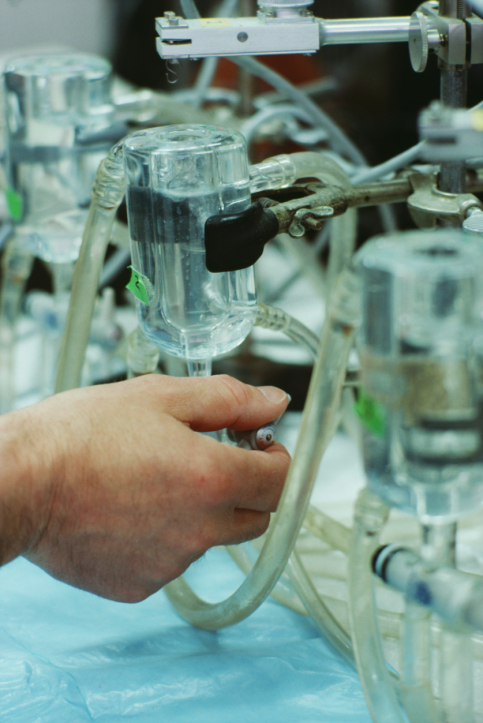
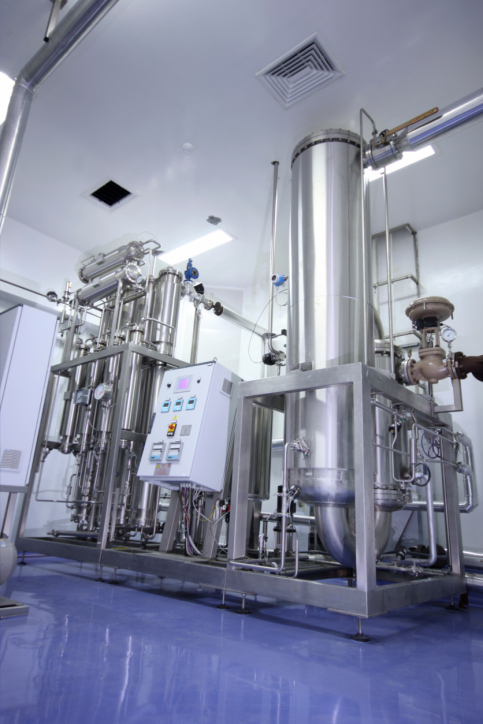
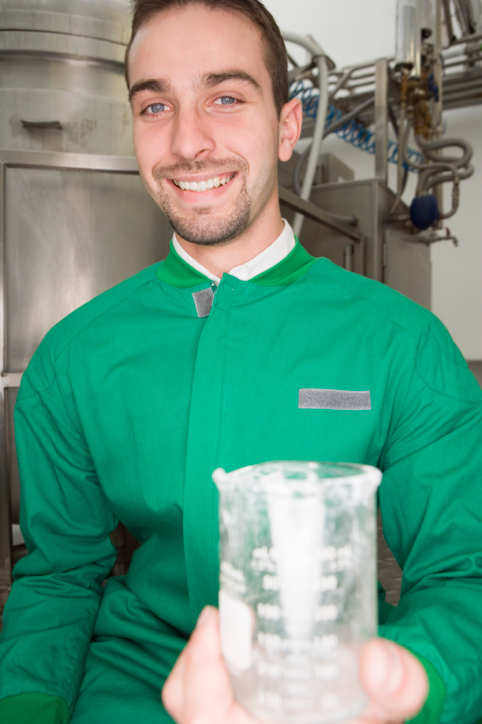
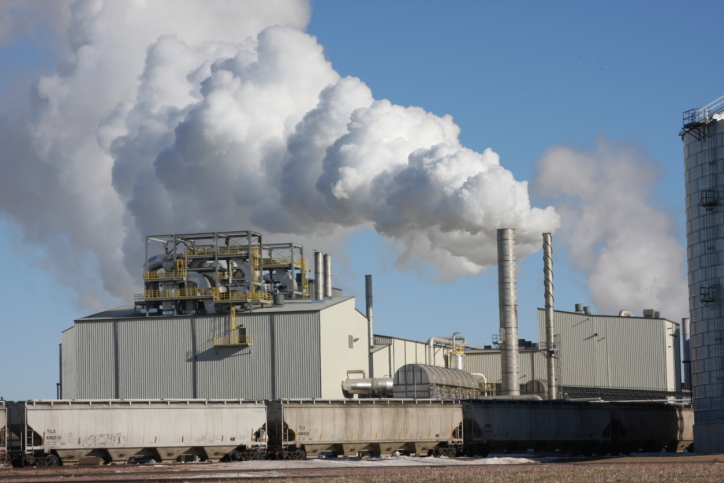
Process Deployment Balance of Plant Engineering
Other clients who are ready to begin selling the new process technology can benefit from our alternative energy fuels solutions and experience by retaining or recommending PROCESS to provide the “balance of plant” process design to effectively integrate the new technology into a customer’s existing plant. This service includes utilities evaluations (wastewater, cooling systems, hot oil, etc.), and site-specific feed stream conditioning in the customer’s existing process, thus allowing both technology provider and the plant operations teams to focus on their respective areas of expertise and business.