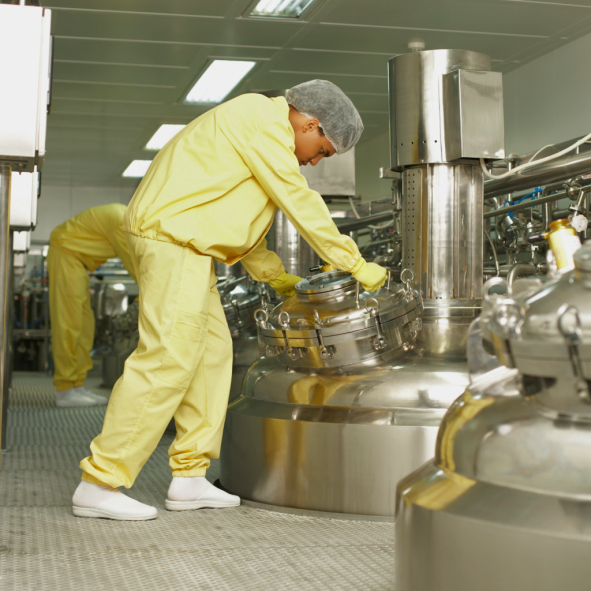
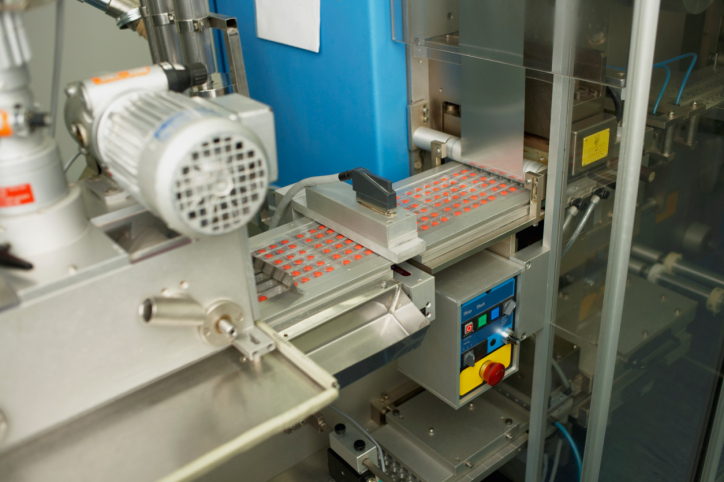
Process Challenges and Applications
Although the majority of the pharmaceutical world is firmly grounded in batch operations, there are many opportunities where good process design skills can yield ample rewards for the client. If you are simply blending a powdered active ingredient (AI) and making pills, then you probably don’t need our services. However, if you are facing some real process challenges, then we can help. As your preferred supplier of Process Engineering services and pharmaceutical process design solutions, we are committed to helping clients comply with all cGMP procedures as described in 21 Code of Federal Regulations, Parts 210 and 211.
How many times have we heard pharmaceutical clients tell war stories of how the design specifics to allow for proper cGMP cleaning was an afterthought and/or was assigned to a junior engineer with little experience? The end result is installed piping and equipment that doesn’t support cGMP compliance and brand-new equipment and piping has to be pulled out, modified, and re-installed at additional time, expense, and unnecessary aggravation. PROCESS has senior level process engineers who can see that these details are properly thought through, addressed, and proper equipment/piping configurations are specified before the design goes into the whirlwind of multi-discipline detail engineering design.
Below are some potential applications areas where PROCESS can assist
Solvent Selection and Substitution
As pharmaceutical manufacturers have known for some time, the easy solvent choices of the past (benzene, methylene chloride) may no longer be viable from either a safety or an environmental perspective. The normal solvent substitutions (mixed xylenes, ethyl acetate, etc.) all bring about their own sets of problems and are not at all without some of their own challenges from the perspective of employee exposure, flammability, or toxicity.
We at PROCESS are experienced with solution thermodynamics and vapor-liquid equilibria of various solvent combinations, and we can assist you in making more benign solvent choices for your active pharmaceutical ingredient (API) synthesis. Our extensive thermodynamic knowledge base can also be useful for multiple phase solvent extractions and final washes and workups.
Process Hazard Analyses
Experience is critical in achieving optimal results within a Process Safety Management (PSM) and Risk Management Program (RMP). Even if your facility may not be mandated to implement such programs, many of the key elements and the rigorous analysis of your process from a safety standpoint can benefit your bottom line in other ways.
Our engineers have performed over 200 PHAs on nearly 300 different processes for over 50 different companies throughout the U.S., Canada, and Puerto Rico. We have also performed over 20 compliance audits thus far. We have performed process safety work in Refining, Petrochemicals, Chemicals, Pulp & Paper, and the Nuclear industry.
PROCESS has a wide range of experience using many of the commercially available software packages for documenting Process Hazard Analyses (PHAs). We also have experience using in-house database programs developed by our customers at the plant or corporate level. This experience means we can quickly and easily apply our knowledge regardless of the software your facility uses.
Hazardous Reactants
Our extensive experience in designing processes for safely handling hazardous reagents or products can assist you in developing and operating a safe manufacturing process. We have experience with gaseous hydrogen, Grignard reagents, methylating agents (dimethyl sulfide, methyl iodide), Raney nickel catalysts, hydrazine, diazomethane, strong acids, oxidizing agents, etc.
FDA 483 Resolutions
Have you had recent FDA audits where you are left with puzzling or problematic 483 issues or concerns? PROCESS may be able to help, especially with those issues related to systematic process deficiencies. As an example, the FDA frequently finds deficiencies in areas such as your United States Pharmacopeia (USP) water supply—frequently caused by weak initial design or installation. PROCESS can help by performing hydraulic analyses of the Clean Steam and Purified Water systems to support your process.
Inventory Management and Control
The efficient FDA-compliant warehouse is a result of careful attention to process design and operation. We can model and simulate flows of incoming quarantined materials awaiting acceptance testing, manufactured intermediates in various stages of completion, and Active Pharmaceutical Ingredients (APIs) awaiting final analysis and release.
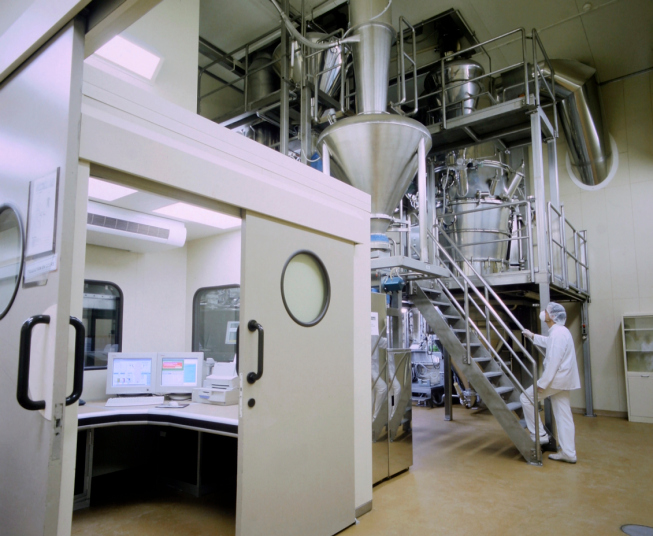
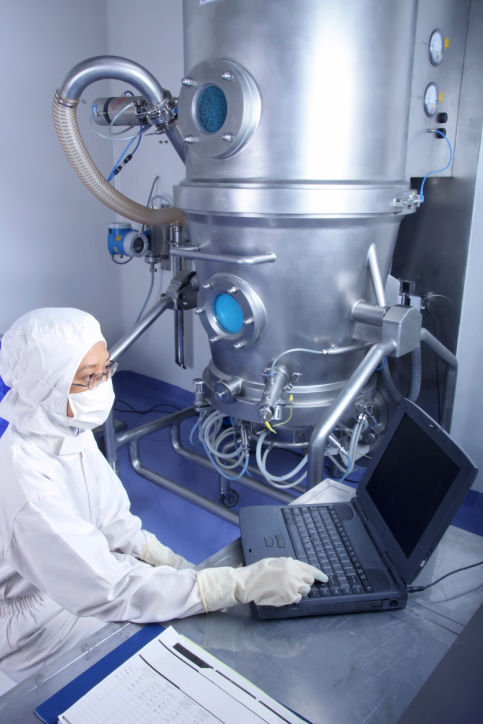
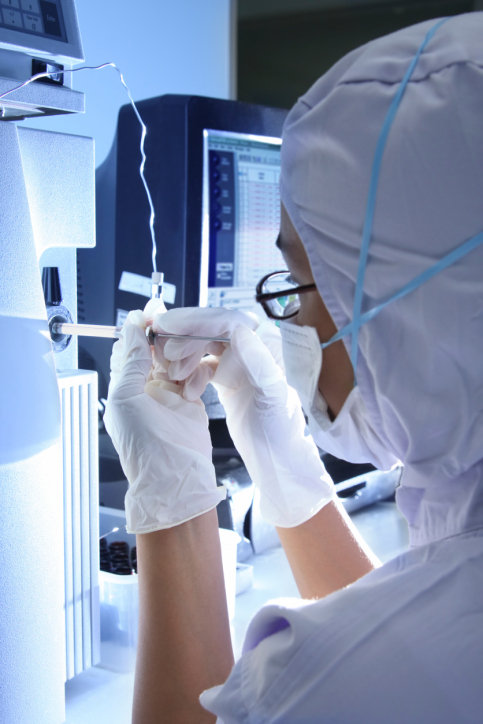
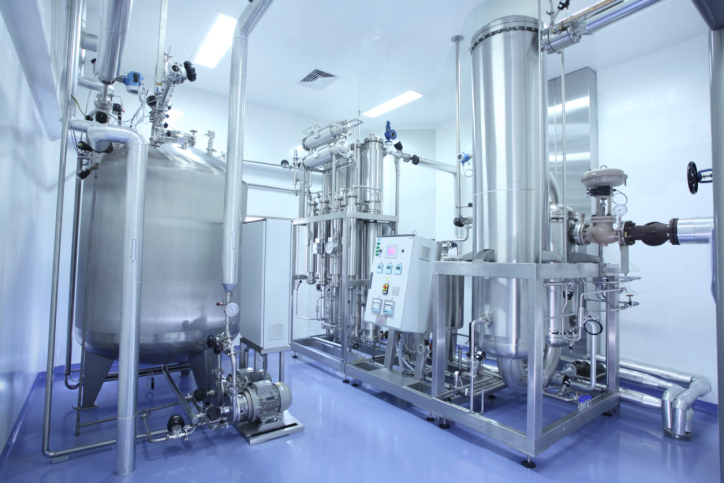
Advanced Process Simulation
It is common practice for engineering firms to use computer process simulation tools to design a new process or model an existing process. The advantages are enormous in terms of predicting the effect of changes, or at evaluating different operation configurations. This obviously allows engineers at the front-end design stage to focus in on a preferred design and reduce the change of wasted capital expenditures and start up time. However, PROCESS has advanced the use of process simulation software by creating Visual Basic linking to Excel spreadsheets for process model inputs and outputs. This means that anyone (operators, accountants, production managers, etc.) can now harness the power of a plant simulation without having to learn how to use the program. The inputs are simply entered into Excel and a low cost “run time” version of the simulation software runs in the background. The results are output in user defined formats. This new capability puts the power of simulation tools in the hands of your front-line production team without having to rely on simulation experts every time a small change needs to be investigated.
Contact us to learn more about our pharmaceutical process design solutions—our experts will be happy to help.