Helping Your Facility Meet NFPA 652/654 and Safely Handle Combustible Dust Hazards
The initial issue of NFPA 652, Standard on the Fundamentals of Combustible Dust, was issued in September 2015. OSHA uses the NFPA standards as the basis for enforcement in managing combustible dust hazards. Are you on track for compliance with the standards?
The following articles may be of interest:
Ventilating Your Processing Area
Helping You With NFPA 652/654
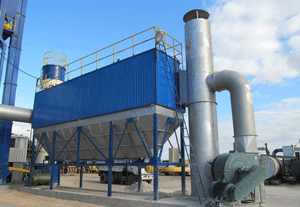
The new standard provides the basic principles of and requirements for identifying and managing the fire and explosion hazards of combustible dusts and particulate solids. Of notable interest is Chapter 7 which introduces the Dust Hazard Analysis (DHA). The DHA is different from other forms of risk assessments such as a Process Hazard Analysis (PHA) as it has narrower requirements of specifically assessing dust hazards. The requirement is retroactive and the new standard does not allow the absence of previous incidents as a basis for deeming a particulate to not be combustible or explosible.
PROCESS can provide clients with a review of their existing particulate solid handling systems to develop a plan for bringing them into compliance with the NFPA 652/654 standards. The development of such information allows the client to confidently and quickly move forward with well-engineered plans to improve the process and meet these standards. Such a project often involves the following tasks:
Site Visit/System Walkthrough
- Visit the facility to review the existing unit operations and layout, to gather technical data such as piping and instrumentation diagrams (P&IDs) and equipment drawings, meet with Operations personnel, and review system operating procedures.
- At this site visit immediate concerns with regard to the NFPA guidelines can be identified and communicated to the client.
Dust Hazards Assessment
- Develop a detailed basis of design/evaluation for the equipment/system handling the particulate solid. This includes determining if there is sufficient information to document that the particulate solid is a combustible dust, and, if applicable, define additional laboratory or field-testing requirements to complete this effort (e.g. physical properties such as combustibility/explosibility, flows, concentrations, etc.).
- Perform a comprehensive review of the information gathered and generated to define how and in what manner the equipment/systems involved pose a potential dust flame, deflagration, or explosion hazard. This assessment must take into account normal operations, normal startup and shutdown procedures, and emergency shutdown situations.
- Define changes to the system that need to be made to mitigate hazards and comply with the NFPA requirements.
Modified System Preliminary Process Design
- Identify and review technically feasible alternatives to upgrade the system and meet the requirements for safe design and operation. This step is critical if there is more than one option that would allow the client to meet certain standards identified during the dust hazards assessment (e.g. install inerting system with controls or upgrade system fan/ductwork). PROCESS can help the client select the best solution based on technical and economic considerations.
- PROCESS then utilizes its experience and ventilation design guidelines to develop preliminary design documents such as red-lined P&IDs, modified system/ductwork layout drawings, collection hood schematics, preliminary hydraulic calculations, process duty level equipment and/or instrumention and control specifications. These preliminary documents are developed to provide a clear understanding of the proposed changes so that they can be effectively reviewed in a formal DHA/PHA.
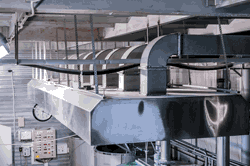
Dust Hazards Analysis (Process Hazards Analysis)
- Perform a node by node risk assessment of the process with the proposed upgrades. Work with the client to rank the degree of hazards for each area so that a strategic plan can be developed for final design of the system. PROCESS can both facilitate and participate in this detailed safety evaluation.
- The objective of the risk assessment is to help ensure all potential scenarios that could result in a dust fire, deflagration, or explosion have been considered and that appropriate mitigation steps have been implemented prior to finalizing design modifications.
- PROCESS can use either a qualitative risk assessment method or a risk-based (semi-quantitative) method, whichever is preferred by the Client.
Modified System Detailed Process Design
- After completion of the DHA, PROCESS will finalize the process design documents for the system upgrades so that the client can move forward with detail design and installation. The detailed process design documents include process-level equipment and instrument specifications, hydraulic calculations, modified P&IDs, process controls description, and preliminary general arrangement drawings.
- PROCESS is often requested by the client to interface with vendors such as ductwork vendors, dust collector vendors, and detailed design firms etc. to assist with the development of the detail mechanical design of the system. This is a critical step as the hydraulic calculations and equipment specifications may need to be updated once mechanical design of the system is complete.
- PROCESS can also assist the client with development of an installed capital cost estimate for the system upgrades for budget planning purposes.