NUCLEAR MATERIALS ENGINEERING SERVICES
A significant portion of PROCESS’ work emanates from the nuclear materials processing industry: nuclear materials production/reprocessing support, process engineering design, environmental compliance, and waste management.
Our plant operations and process design experience is quite extensive and, because our company is focused only on chemical engineering, we are very good and efficient at the nuclear materials engineering services we provide. We have been regularly subcontracted for work supporting the missions of the Oak Ridge National Laboratory (ORNL), the Y-12 National Security Complex, the Savannah River Site, and the Hanford Site. PROCESS has also performed work in support of the Atomic Energy of Canada Limited (AECL) and private nuclear material manufacturers. Projects have been in the areas of design definition and implementation, process design development, specialized computer modeling calculations, operational troubleshooting, and system engineering support. Our work has included the design and operation of processes for various depleted and enriched uranium compounds, including Category II nuclear material as well as associated contaminants and daughter products, and nuclear waste. We are familiar with the stringent requirements associated with the implementation of strict nuclear criticality safety design constraints, conduct of operations, and configuration control management. We have been successful in interactions with oversight organizations such as the Department of Energy (DOE), Nuclear Regulatory Commission (NRC), and the Defense Nuclear Facilities Safety Board (DNFSB).
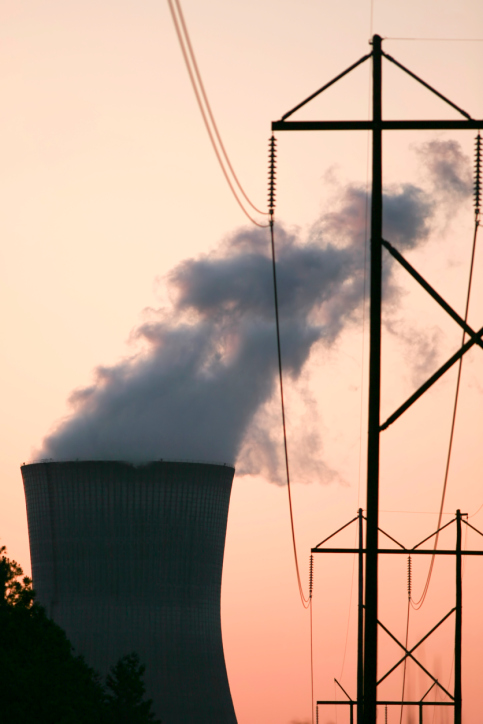
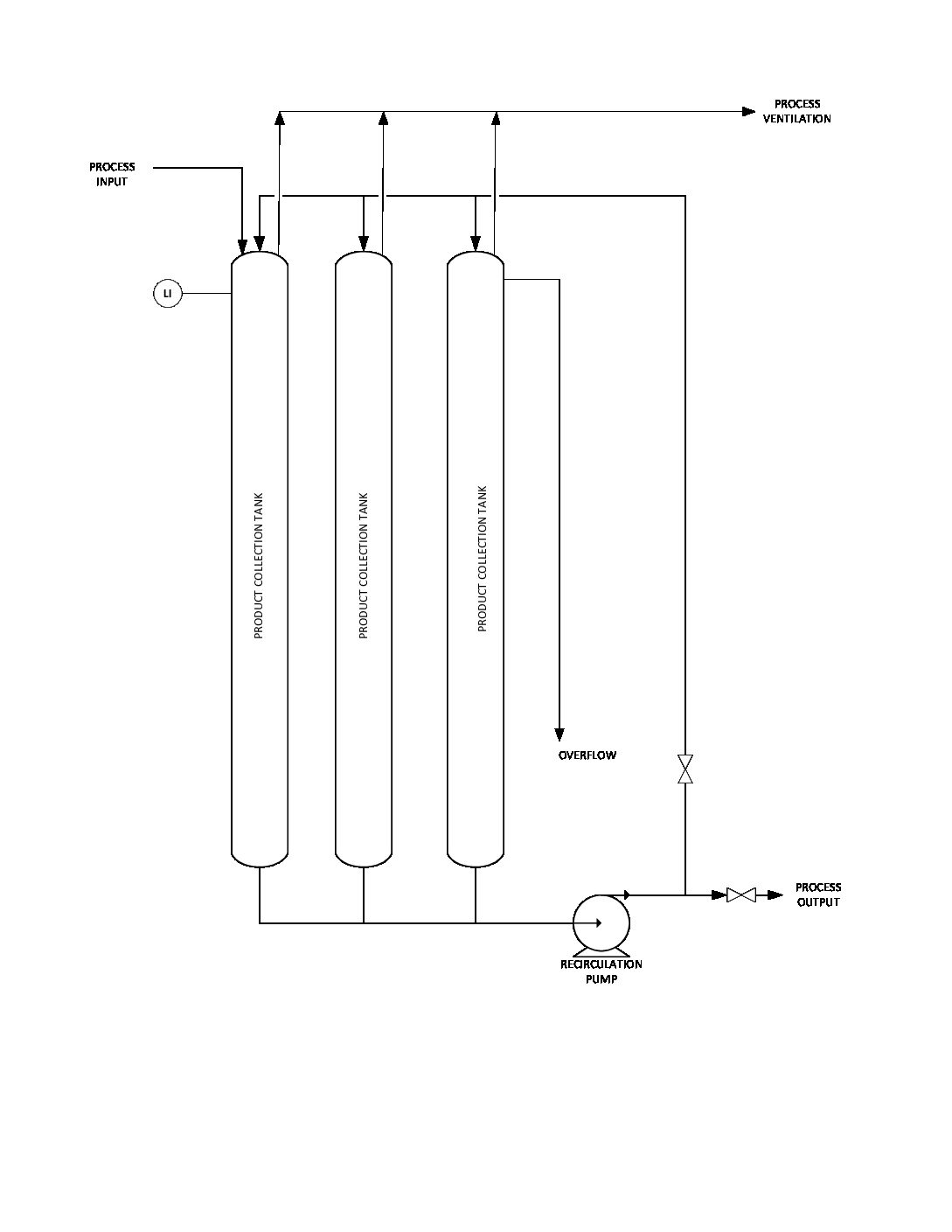
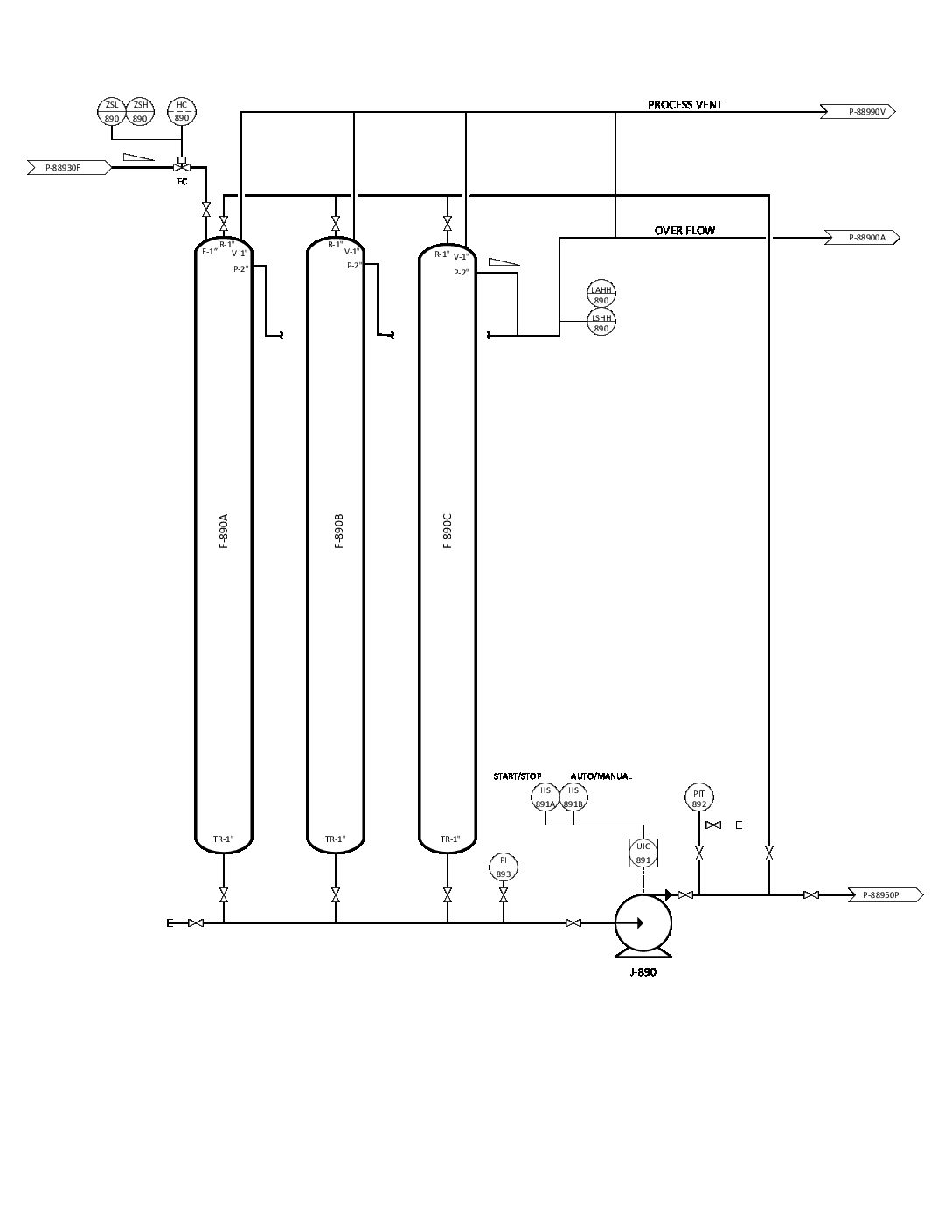
Our Nuclear Niche And Nuclear Materials Services
We address the full spectrum of process engineering services over the system life cycle of a process, from the initial stages of design definition, through detailed process design and operational startup/support, and through decommissioning and closure. The effective use of process engineering as a discipline, when utilized throughout the process lifetime, can serve as an integrating discipline to help ensure that the technical baseline is defined and maintained.
Process Design Definition: Definition of the overall process system and technical requirements, predicting expected process behavior through modeling and simulation, evaluating viable alternatives. Process design provides the roadmap / blueprint for other design disciplines to follow.
- Strategic planning support
- System Requirements Document (SRD)
- Technical baseline development
- Design Criteria development support
- Feasibility /alternatives study
- Block Flow Diagrams (BFDs)
- Conceptual design
- Process simulation and analysis
- Material and Energy balances
- Process Flow Diagrams (PFDs)
- Process Hazard Analyses (PHA)
- Safety basis development
- Integrated Safety Analysis (ISA) support
- NRC Licensing support
Detailed Process Design: Process flowsheet is refined and design details are developed. This stage of design is highly interactive between design disciplines, with the process discipline responsible for helping to ensure the process baseline remains in compliance with the established design criteria.
- Piping & Instrumentation Diagrams (P&IDs)
- System Design Description (SDD)
- Waste management plans
- Environmental compliance reviews
- Nuclear Criticality Safety design implementation
- Safety basis implementation
- Equipment specifications and datasheets
- Hydraulic flow calculations
- Design Analysis Calculations (DACs)
- Compliance with NQA-1 standards
- System integration
- Interface coordination
- HAZOP detailed analysis
- Quality Level assessment and assignment
Operational Planning: Anticipating operational needs, PROCESS reviews the on-going design with an operating eye as it is implemented during construction.
- Operating Mode Summary (OMS)
- Bottleneck analysis
- Vendor package review
- Conduct of Operations planning
- Project Change control
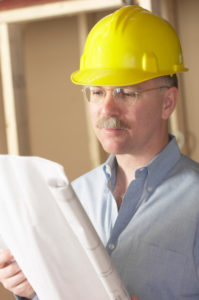
Startup Operations: Field support of operating the process requires an understanding of how a process works and what its safety envelope is. PROCESS is experienced in establishing and protecting the technical baseline of the process.
- Operating procedures for normal and abnormal conditions
- Test procedures
- Operational Readiness Review (ORR) preparation
- Field startup testing
- Unresolved Safety Determinations (USQDs)
- System verification
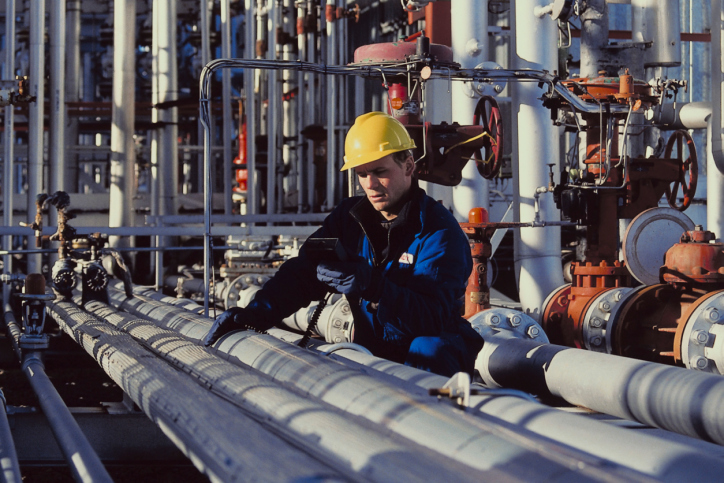
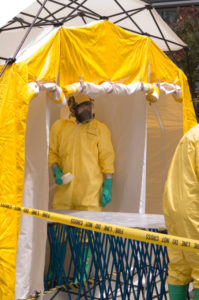
Operations and Decommissioning: Continual improvement of operations may result in system expansions or process shutdowns. Such system changes can be implemented in a logical manner which minimizes the downtime of interfacing processes.
- Process assessments
- Conduct of operations implementation
- Occurrence reporting input
- RadWorker experience
- Decommissioning
- Hazard evaluations
- Shutdown / decommissioning procedures
- Field oversight activities
PROCESS has provided these services to DOE and AECL facilities and nuclear production sites in both the commercial and government realms. Our Q-cleared engineers have extensive DOE and NNSA experience providing chemical process design, process modeling and simulation, startup operations support, ongoing operational troubleshooting / optimization, and decontamination & decommissioning support. We are familiar with stringent Conduct of Operations and Project Control procedures, have created, implemented, and maintained Safety Authorization and Technical Basis documentation, and have successfully interacted with the Defense Nuclear Facilities Safety Board and other stakeholder organizations.
A Great Project Partner for Detail Engineering Companies
PROCESS is not a placement agency or loose group of consultants, we are a specialized engineering firm. Our engineers have performed client work under task-specific, staff-augmentation, and seconding subcontracts. On average our process engineers have over 20 years of experience and all of them have some background in plant operations which we feel is an invaluable asset to our clients.
We offer the full spectrum of process chemical engineering services for nuclear processes at several different commercial and government sites.
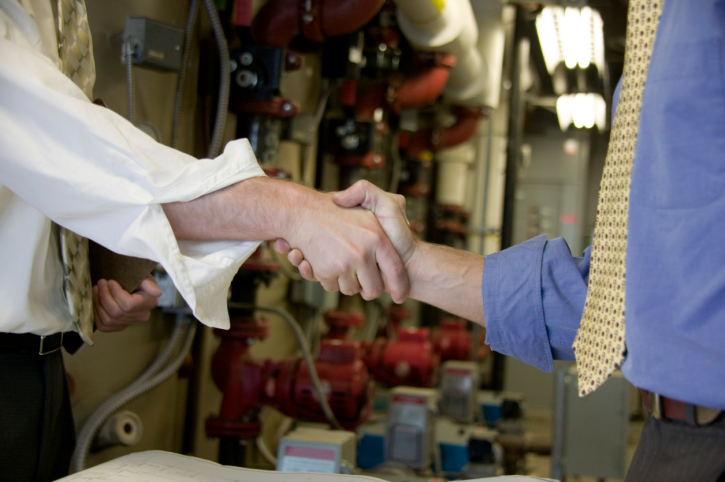
RESEARCH FACILITIES
Research Facilities Present Special Challenges
PROCESS has significant experience in performing process engineering services for a number of different research facilities. In some ways these projects are similar to working with companies trying to develop and commercialize a new technology; what they are trying to achieve has typically not been done before and there are some unique challenges, there are often more concepts than firm answers when it comes to defining how a particular system may work, and the client needs someone with significant and a varied experience base to guide them through the process evaluation/development/design/startup. Some of the unique challenges R&D facility projects present are invariably associated with the design and management of process parameters under abnormal or extreme cases not typically seen in the commercial processing world. Projects like this require a level of analysis far beyond what is required to design a simple distillation system BUT they are still problems that can be solved by the correct application of basic chemical engineering principles. Here are only a few examples of some of the special challenges we have encountered:
- designing proper hydraulics for critical cooling water systems in the ml/hour flow range to properly cool multi-million dollar, one-of-a-kind research equipment
- designing processes to control pressures to within +/- 0.0005 psig
- designing systems to remove or separate unusual compounds
- designing special safety systems not typically found in industrial applications.
Here are a few of the development phases where PROCESS can assist R&D facility clients:
- High level process technology review (feasibility study) to make sure a proposed process idea is feasible and does not violate physical and thermodynamic laws
- Provide a screening study to help narrow down the best possible process options to work along side your developed technology for a particular application
- Provide the necessary balance of plant design around a particular technology or equipment
- Provide process engineering consulting to help build in proven processing concepts for an efficient and reliable process or equipment design
- Create a custom detailed process simulation that validates the process and acts as a repository for all critical process information
- Provide independent engineering validation commentary along with associated engineering documents (PFDs, H&MBs, etc.) to convince the stakeholder that a process is real and viable…or not
- Spreadsheet simulation tools that allow someone not trained in process simulation to make changes to process parameters such as feed composition, rates, etc. and view the results. These tools can also provide economic analysis numbers such as operating costs, energy usage, ROI, and more for various trials that may be considered for testing
- Provide Pilot Plant, Demonstration Plant, or Semi-works scale process design packages (Design Basis, Simulations, H&MBs, PFDs, Equipment Specs, P&IDs, Controls Description, Cost Estimates, etc.)
- Provide pilot test plans and pilot testing oversight
- Help estimate key physical property information that may not be known
- Provide process engineering support at any phase of the project
- Provide scale-up process designs for scaling up your process from lab to pilot, pilot to demonstration, or demonstration to commercial size.
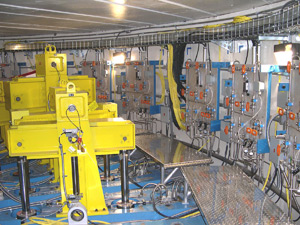
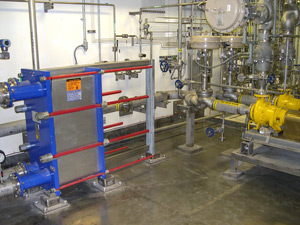
Seeing Your Technology Implemented
Forming a trusted relationship with PROCESS puts you in a position to confidently evaluate and develop your research facility’s processes as program needs change. Utilizing PROCESS as your process engineering partner helps ensure, from a process standpoint, that your systems will be effective, efficient, and operate very reliably for your scientific operating staff.
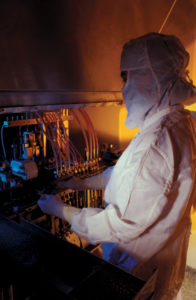
EXPLOSIVES / MUNITIONS / PROPELLANTS
ENERGETIC MATERIALS PROCESS ENGINEERING SERVICES
A significant portion of PROCESS’ work has grown out of the nuclear materials processing industry: nuclear materials production/reprocessing support, process engineering design, environmental compliance, and waste management. Our experience in this nuance chemical processing industry opened the door for PROCESS to begin performing work for multiple government owned, contractor operated, production facilities supporting US military munitions manufacturing.
Our plant operations and process design experience are quite extensive and, because our company is focused only on chemical engineering, we are very good and efficient at the energetic materials engineering services we provide. We have been subcontracted for work supporting the missions of the Department of Defense, Department of the Army, the United States Army Corps of Engineers, and the Dept of the Navy, etc. at various plant facilities throughout the US including both production and research facilities. Projects have been in the areas of design definition and implementation, process design development, specialized computer modeling calculations, operational troubleshooting, and system engineering support. Our work has included the design and operation of processes for various energetic materials, including explosives, munitions, and propellants related materials along with their solvents, byproducts and waste streams. We are familiar with the stringent requirements associated with the implementation of strict conduct of operations and configuration control management.
Our Services Niche
We address the full spectrum of process engineering services over the system life cycle of a process, from the initial stages of design definition, through detailed process design and operational startup/support, and through decommissioning and closure. The effective use of process engineering as a discipline, when utilized throughout the process lifetime, can serve as an integrating discipline to help ensure that the technical baseline is defined and maintained.
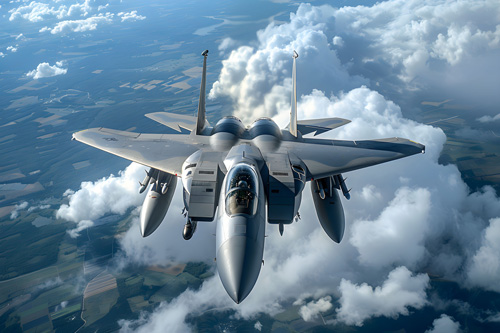
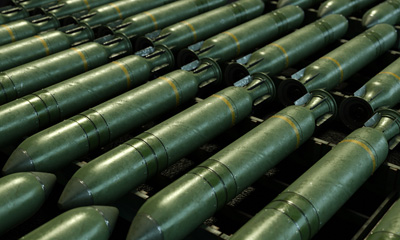
Process Design Definition: Definition of the overall process system and technical requirements, predicting expected process behavior through modeling and simulation, evaluating viable alternatives. Process design provides the roadmap / blueprint for other design disciplines to follow.
- Strategic planning support
- System Requirements Document (SRD)
- Technical baseline development
- Design Criteria development support
- Feasibility study
- Technical & Economic process alternatives evaluations
- Block Flow Diagrams (BFDs)
- Conceptual design
- Process simulation and analysis
- Material & Energy balances
- Process Flow Diagrams (PFDs)
- Process Hazard Analyses (PHA)
- Safety basis development
- Integrated Safety Analysis (ISA) support
- Facility environmental permitting support
Detailed Process Design: Process flowsheet is refined and design details are developed. This stage of design is highly interactive between design disciplines, with the process discipline responsible for helping to ensure the process baseline remains in compliance with the established design criteria.
- Piping & Instrumentation Diagrams (P&IDs)
- Controls system functional specification
- System Design Description (SDD)
- Waste management plans
- Environmental compliance reviews
- Criticality Safety design implementation
- Safety basis implementation
- Equipment specifications and datasheets
- Hydraulic flow calculations
- Design Analysis Calculations (DACs)
- Compliance with standards
- System integration
- Interface coordination
- HAZOP detailed analysis
- Quality Level assessment and assignment
Operational Planning: Anticipating operational needs, PROCESS reviews the on-going design with an operating eye as it is implemented during construction.
- Operating Mode Summary (OMS)
- Bottleneck analysis
- Vendor package review
- Conduct of Operations planning
- Project Change control
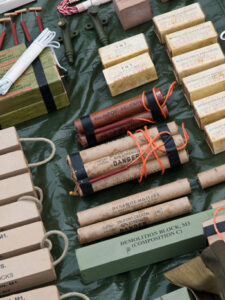
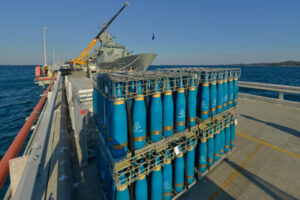
Startup Operations: Field support of operating the process requires an understanding of how a process works and what its safety envelope is. PROCESS is experienced in establishing and protecting the technical baseline of the process.
- Operating procedures for normal and abnormal conditions
- Test procedures
- Operational Readiness Review (ORR) preparation
- Field startup testing
- Unresolved Safety Determinations (USQDs)
- System verification
Operations and Decommissioning: Continual improvement of operations may result in system expansions or process shutdowns. Such system changes can be implemented in a logical manner which minimizes the downtime of interfacing processes.
- Process assessments
- Conduct of operations implementation
- Occurrence reporting input
- Decommissioning
- Hazard evaluations
- Shutdown / decommissioning procedures
- Field oversight activities
PROCESS has provided these services to energetic materials production facilities in both the commercial and government realms. Our process engineers have extensive experience providing chemical process design, process modeling and simulation, startup operations support, ongoing operational troubleshooting / optimization, and decontamination & decommissioning support. We are familiar with stringent Conduct of Operations and Project Control procedures, have created, implemented, and maintained Safety Authorization and Technical Basis documentation.
Process Safety Services Overview: PROCESS’ process safety and risk management services help our clients meet their safety, health, and environmental compliance needs in a thorough, systematic, and efficient manner. We have the experience to address issues ranging from operational risk, equipment integrity, loading limits or naturally occurring hazards.
Our safety services include, but are not limited to:
- Facilitating Process Hazards Analyses (PHAs)
- Hazards Assessments (including HAZOPs)
- Conducting Process Safety Compliance Audits
- Layer of Protection Analyses (LOPA)
- Conducting Safety Integrity Level (SIL) selection analyses for Safety Instrumented Systems (SISs)
- Dust Hazards Analyses
Training Classes Offered:
- Resolving/Implementation Assistance of PHA Recommendations
- Developing Process Safety Information
- Developing Process Safety (PSM) & Risk Management (RMP) Programs
A Great Project Partner for Detail Engineering Companies
PROCESS is not a placement agency or loose group of consultants, we are a specialized engineering firm. Our engineers have performed client work under task-specific, staff-augmentation, and seconding subcontracts. On average our process engineers have over 25 years of experience and all of them have some background in plant operations which we feel is an invaluable asset to our clients.
We offer the full spectrum of process chemical engineering services for energetic materials processes at several different commercial and government sites.
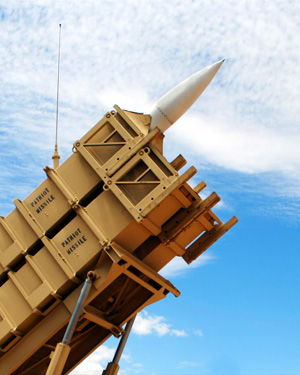
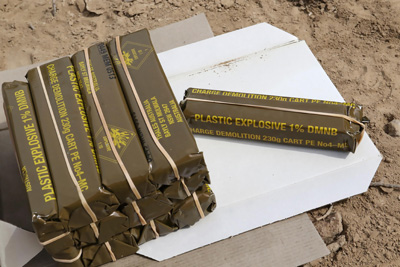