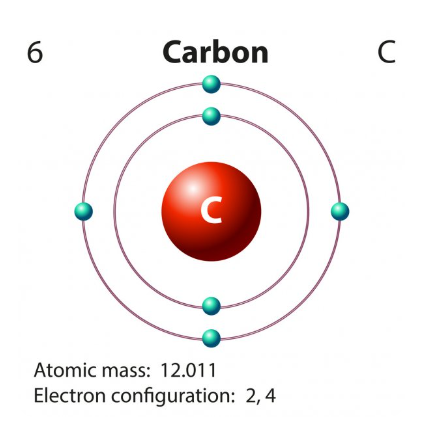
Adsorption on Activated Carbon – Part 1, M. Tanzio 09/10/20
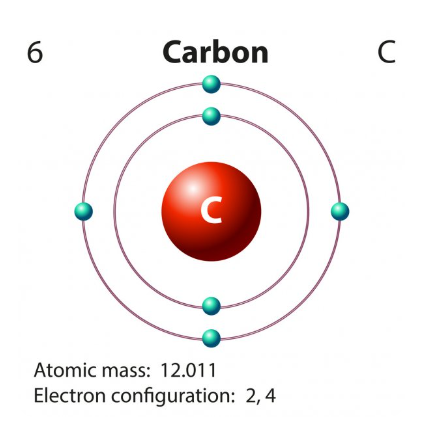
Background
As a unit operation, many do not consider Adsorption a glamorous technology – “just put some charcoal in a drum and away you go!”. But the physics involved and the engineering required for an effective system are quite challenging and sophisticated.
For a long time the unit operation of Adsorption has been a cost effective method for separating molecular components (Reference 1). Since the fifteenth century, it was known that the color of solution liquids could be improved by adsorption with various materials. In the late eighteenth century, sugar solutions were decolorized using bone char, and air for hospital respirators was purified in the nineteenth century utilizing wood charcoal.
Today, Adsorption is widely used for many molecular separations in the petroleum, natural gas, petrochemical, chemical and food industries. The most commonly used adsorbent material classes include molecular sieve zeolites, activated alumina, silica gel and activated carbon.
This blog will focus on just some of the important aspects of adsorption on activated carbon in the process industries and serves as an introduction to the topic. The references cited at the end of this article are good starting points for further information.
We will cover this topic in two parts. Part 1, to be covered this month, will discuss:
Activated Carbon
Activated carbon is available as powders, granules and pellets. and is commonly used to:
- reduce Volatile Organic Carbons (VOCs) and other air pollutants from process off-gases;
- reduce water pollution from process waste waters;
- purify off-gas for product recovery and downstream process use;
- remove contaminants from liquid products;
- protect downstream equipment (reactor beds, ion exchange equipment, etc.).
Activated carbon is classified as an amorphous, hydrophobic adsorbent (Reference 4). The extent of hydrophobicity of an activated carbon depends on its ash content and its level of surface oxidation. This type of adsorbent is a microcrystalline, non-graphitic form of carbon with internal surface area from about 400 m2/gm to 1800 m2/gm. It can be made from different materials depending on whether the activated carbon is used in a gas system or a liquid one. The properties of an activated carbon (hardness, density, pore size, particle size, surface area, extractables, ash, pH) depend on the starting raw material from which it is made. These properties are varied and optimized for a particular service. For decolorizing liquids, wood, peat, lignite and lignin are the usual starting materials. For use in gas phase systems, nutshells, coal, peat and petroleum residues have been used. Other materials used to produce activated carbon include: animal blood and bones, rice hulls, coconut husks, coal tars, pitches and carbon black.
Carbon activation is usually accomplished by pyrolyzing (carbonization or calcination) the starting material at a temperature of 400 °C to 500 °C to remove all volatile material leaving only the carbon. Depending on the application, the carbon is then partially oxidized to provide the required porosity and surface area. Inorganic chemicals are sometimes used to dehydrate the organic molecules during the pyrolysis step. Oxidation can be achieved by using:
- Air at low temperature;
- High temperature steam, flue gas or carbon dioxide
- Oxidizing agents (alkali metal hydroxides, carbonates, sulfates, phosphates).
Typical physical properties, taken from Reference 4, for carbon adsorbents:
Material | Internal Porosity (%) | Bulk Dry Density (kg/L) | Avg. Pore Diameter (nm) | Surface Area (km2/kg) | Dry Sorptive Capacity (kg/kg) |
Shell-based | 60 | 0.45 – 0.55 | 2 | 0.8 – 1.6 | 0.4 |
Wood-based | ~80 | 0.25 – 0.30 | 0.8 – 1.8 | ~0.7 | |
Petroleum-based | ~80 | 0.45 – 0.55 | 2 | 0.9 – 1.3 | 0.3 – 0.4 |
Peat-based | ~55 | 0.30 – 0.50 | 1 – 4 | 0.8 – 1.6 | 0.5 |
Lignite-based | 70 – 85 | 0.40 – 0.70 | 3 | 0.4 – 0.7 | 0.3 |
Bituminous-coal-based | 60 – 80 | 0.40 – 0.60 | 2 – 4 | 0.9 – 1.2 | 0.4 |
Synthetic polymer based (pyrolyzed) | 40 – 70 | 0.49 – 0.60 | 0.1 – 1.1 | ||
Carbon molecular sieve (air separation) | 35 – 50 | 0.50 – 0.70 | 0.3 – 0.6 | 0.5 – 0.2 |
For specific applications, and to improve removal efficiency, activated carbon can be chemically treated or impregnated. Impregnated activated carbon adsorbs and retains the specific components long enough for the chemical impregnant to react with the contaminant component (chemisorption). Impregnated activated carbon has been specially designed to collect chemical components that are difficult to adsorb with standard activated carbon.
Systems used for carbon adsorption come in three basic types:
- filled cartridges (carbon canisters)
- packed, fixed beds
- powdered carbon injection.
Pre-packed filter cartridges are usually used in low-load applications and can be periodically replaced after their working capacity is reached. When a large quantity of activated carbon is required, such as for heavily-loaded systems, a fixed bed of granular activated carbon can be used. For high flow rate streams with a low concentration of the component to be removed (dioxin removal, for example), powdered activated carbon can be injected into the stream. The spent powder, containing the adsorbed material, is then filtered away.
Vendors can offer these systems as pre-packaged, modular units. Fixed beds and carbon cannisters are discussed further later in this article.
Activated carbon which has reached its working capacity can be either regenerated for re-use or disposed and replaced with fresh carbon. Regeneration can be done on-site at the plant, or can be shipped to a central regeneration facility. Various regeneration methods are discussed next month in Part 2.
Some Important Process Parameters
Many process parameters and phenomena are important for designing a carbon adsorption system:
- Pressure, temperature, flowrate, and contaminant concentration
- Flow direction
- Carbon particle physical properties (hardness, density, shape, pore size, particle size, surface area, extractables, ash)
- Batch vs continuous operation
- Equipment capacity
- Desired recovery
- Cycle times
- Sorption Equilibrium
- Contaminant solubility in a liquid
- Contaminant molecular weight
- Moisture content and humidity of the feed
- Solution pH
- Adsorbent deactivation
- External and internal heat and mass transfer
- Hydrodynamics including axial and radial dispersion and pressure drop
- Reaction kinetics.
The references cited present additional information on adsorption theory, phenomena modeling and the effects of other process parameters on carbon adsorber design. Equipment vendors should also be consulted.
For this short discussion, we consider only two critical parameters:
- Capacity
- Particle size.
Carbon bed capacity is an important process parameter which can cause some confusion. There are several types of capacities important for adsorber design:
- Saturation Capacity
This is the maximum capacity the adsorbent can hold. It should NOT be used alone to size the bed or to compare different carbon adsorbent materials.
- Breakthrough Capacity
This capacity is defined as the amount of material that is actually adsorbed before a concentration of the material exits, or breaks through, the bed that reaches either a limiting pollutant, toxic, or flammable concentration.
The required breakthrough capacity could vary from locality to locality depending on regulations and safety concerns.
- Heel Capacity
This is the amount of adsorbed material remaining in the bed after regeneration.
- Working Capacity
This capacity is the difference between the breakthrough capacity and the heel capacity after the bed has been “conditioned”. It is the amount of material actually adsorbed in each working cycle.
Before a stable amount of material can be adsorbed and regenerated, the bed usually must go through a number of operating conditioning cycles. About five cycles are required but should be confirmed with the equipment vendor. After conditioning, the carbon may only adsorb about 50% of the amount that was adsorbed by the starting virgin material. This is thought to be the result of continued recapture of molecules (i.e., depressed vapor pressure) in the carbon micro-pores. Molecules, especially VOCs, have a difficult time desorbing from the carbon micro-pores.
This conditioning effect on working capacity must be considered when sizing the adsorbent bed. The conditioning effect can require up to twice as much adsorbent in the bed and will have a significant effect on installation, operating, and maintenance costs. Pilot plant or lab testing by the equipment vendor may be required.
The time required for breakthrough depends on the bed size. So does the time required for regeneration. Both conditioning and regeneration requirements need to be carefully considered when choosing the number of beds and the bed dimensions. The facility design would also need to consider the longer breakthrough times during the initial conditioning cycles of the virgin carbon material.
The working capacity is the capacity to be used for sizing the bed. A typical working capacity is 10-20 pounds of contaminant per 100 pounds of carbon but can vary depending on the application.
Another important parameter is particle size. Two considerations affect the choice of adsorbent particle size:
- system pressure drop
- mass transfer characteristics.
Pressure drop through a fixed bed can be reduced by choosing a large particle size. But the smaller the particle size, the greater the mass transfer rate and the less adsorbent required. This trade-off needs to be considered.
The trade-off is especially important for gas phase systems where compression costs can be significant. Compression costs need to be considered when determining the optimum vessel diameter. Typically, when only considering the mechanical design of the vessel, an optimum vessel diameter is obtained for a fixed quantity of adsorbent based on material stress and L/D ratio. The optimum diameter increases with decreasing pressure for this case.
But for a fixed quantity of adsorbent, the pressure drop also decreases with an increase in bed diameter. By considering the compression costs, the optimum vessel diameter could be larger than that dictated by mechanical stress conditions alone.
Types of Processes
Processes exist for treating both gases and liquids in carbon systems. Carbon used to treat a gas phase fluid usually contains a larger number of small pores than that used to treat a liquid phase. Carbon systems are also used for treating liquid streams, however, it is very difficult to predict how effective carbon will be in treating a given liquid (Reference 6). Laboratory tests are necessary and consists of two parts:
- Preliminary isotherm tests to demonstrate the feasibility of using a carbon system
- Laboratory column tests to obtain data for designing the commercial plant.
Tests for water-related applications may take several months. But most testing for chemical applications take less than a month (Reference 6).
The following types of adsorption equipment are used:
- Fixed regenerable beds;
- Disposable/rechargeable cannisters;
- Traveling bed adsorbers;
- Fluid bed adsorbers;
- Chromatographic baghouses.
For air pollution control, the most commonly used equipment are fixed-bed systems and cannister types. Since these are the most used equipment types, only they will be discussed here. Information on the other types of equipment can be found in the References.
Fixed Bed Units
Fixed-bed adsorbers can operate intermittently or continuously depending on the operation of the feed source.
In intermittent operation, the adsorber removes contaminant only during the time which the feed source is emitting contaminant. After the the feed source is shut down (e.g., overnight), the unit begins the desorption cycle. When desorption is complete, the bed sits idle until the feed source starts up again.
For continuous operation, the feed source operates continuously and a regenerated carbon bed must always be available for adsorption. At least two carbon beds are provided. One is adsorbing while the other one is desorbing or idled. Since each bed must be capable of adsorbing the entire contaminant loading, twice as much carbon must be provided than an intermittent operation. If the adsorption and desorption cycle times are significantly different, three, four, or even more beds may be required.
For some units, the process conditions during regeneration are much more severe than those during adsorption. A single regenerator with materials of construction capable of handling the more severe conditions may be more cost effective than to make all adsorbers capable of regeneration by using the more expensive material of construction. Most water and wastewater treatment processes using thermally reactivated carbon utilize a separate vessel dedicated only to the regeneration step.
Carbon Cannisters
Cannister-type adsorbers are relatively small, returnable containers and include carbon beds made from 55-gallon drums. However, systems as large as 18,000 cfm are available in the industry (Reference 2). Cannisters are normally used for lower-volume, intermittent feed sources (for example, storage tank vents), where off-site regeneration is available and economical.
Carbon cannisters are not intended for on-site desorption. The spent carbon is usually sent to a central facility to be regenerated or disposed. Either the carbon or the entire cannister is replaced.
Most systems use two or more cannisters in series. Two or more parallel trains may also be specified.
Next month, in Part 2, we will discuss:
- Regeneration and disposal methods;
- Some tips to keep in mind when designing a carbon adsorption system.
References
- R.W, Rousseau (ed.), “Handbook of Separation Process Technology”, Chapter 12 by G.E. Keller II, R.A. Anderson, C.M. Yon, “Adsorption”, Wiley & Sons, 1987.
- “EPA Air Pollution Control Cost Manual”, W. M. Vatavuk, W. L. Klotz, R. L. Stallings, EPA/452/B-02-001, Section 2/ Chapter 1 “Carbon Adsorbers”, 09/1999.
- CATC TECHNICAL BULLETIN, “CHOOSING AN ADSORPTION SYSTEM FOR VOC: CARBON, ZEOLITE, OR POLYMERS?”, EPA-456/F-99-004, May 1999.
- Perry’s Chemical Engineer’s Handbook, Section 16, Adsorption and Ion Exchange, 7th Edition, McGraw Hill, 1997.
- Wauquier, Jean-Pierre. (2000). Petroleum Refining, Volume 2 – Separation Processes. Editions Technip. A. Deschamps, S. Jullian Chapter 10: “Adsorption”;
- Cheremisinoff, Nicholas P.. (2000). Handbook of Chemical Processing Equipment. Elsevier. Chapter 5.3: “Adsorption”.
- Albright, Lyle F.. (2009). Albright’s Chemical Engineering Handbook – Taylor & Francis. K.S. Knaebel, Chapter 14: “Adsorption”.
- DG 1110-1-2, DEPARTMENT OF THE ARMY, U.S. Army Corps of Engineers, Engineering and Design, “ADSORPTION DESIGN GUIDE” , 03/01/2001.
- D.D. Randall, K.S. Schaffner, Section 3.1 / Chapter 1, “Carbon Adsorbers”, 10/2018.