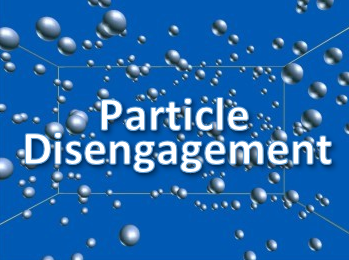
written by Michael Tanzio, Process Engineering Associates, LLC; February 2021
The industrial literature is full of stories about poor separation in systems consisting of drops or particles in a separate continuous phase (gas or liquid). Poor disengagement of the dispersed phase can lead to major, unwanted, economic consequences (poor product quality, reduced throughput, environmental and safety consequences, plugged piping, damaged equipment, etc.). Many times, this poor performance can be traced to the following:
- Use of poor design methods for sizing the separation vessel
- Lack of complete and valid information on the system (volume fraction of dispersed phase, particle size distribution, particle shape and density, etc.).
But how do you know a design method is poor? Or what data and information is required for a high-quality design? These can be answered, in part, by understanding the assumptions and limitations inherent in the design method being used. If the assumptions and limitations for the system is within those of the design method, then your design is probably working. If not, then you are probably reaching for your wallet!
For this discussion “particle” refers to both solid particles and liquid drop particles.
The majority of disengagement calculation methods are limited by the following assumptions inherent in the calculations:
- The particles are rigid, undistorted spheres.
- The drag force is the major force contributing to momentum exchange between the phases. Particle rotation (Magnus lift force), gradient forces (concentration, velocity (Saffman force), pressure, temperature), virtual mass effects, Basset force effects, collisional forces, electrostatics, all friction, viscous stress and turbulent stress are neglected (references 15, 16).
- The fluid system is dilute with the particles existing at very low volume fractions in the total fluid.
- The continuous phase is a quiescent fluid and relative velocity is negligible.
- The particles are not hindered in their settling by other particles.
- Dispersion bands are not considered.
- The fluids are Newtonian.
- The particles are larger than the mean free path of the continuous gas phase and Brownian motion is not important.
- Wall effects on particle settling are negligible.
- There are no phase changes or mass transfer occurring in the vessel.
A number of other assumptions also limit the use of many design methods. The ones listed above are considered the major factors limiting current design methods.
Although these assumptions should satisfy the majority of the systems analyzed, there may be cases where these assumptions are not valid. A qualitative discussion of some of these effects is presented next with some guidance on when they should be considered. References are also cited for further information.
Particle Distortion
The equations used to estimate terminal velocity are for rigid, spherical particles in a stagnant medium. However, liquid drops in motion may not be rigid or spherical. Up to a certain transition drop size, the terminal velocity can be higher than estimated due to internal circulation within the drop. As the drop size increases, a transition point is reached where the drop starts to oscillate and distort from a spherical shape. At this transition, the terminal velocity is a maximum and starts to decrease as the drop size gets larger.
Complicating the phenomena are the effects that contaminants or surfactants may have on the internal circulation and drop distortion. The demarcation between a spherical particle and a distorted particle is a function of both the Eotvos (Eo) number and particle Reynolds (Re) number. Below a particle Re of about 1.2, particles should remain spherical at all Eo numbers. At Eo numbers greater than about 0.4, particle distortion may be important. Either the Clift correlation (References 1 and 2) or the Hu & Kintner correlation (Reference 3) can be used to estimate the effect of particle distortion.
Dilution and Hindered Settling
The majority of design methods assume the concentration of drops in the dispersed phase is very low. These methods are probably valid only for dispersed phase volumetric hold-ups below 0.03 in the Stoke’s regime and below 0.05 in the Newton regime. This is due to two factors:
- As a design requirement, many current design methods set the maximum superficial velocity of the continuous phase to be equal to the terminal velocity of a single particle in a stagnant fluid. However, the real velocity of the continuous phase is the proper velocity to use, and, in a moving fluid, the drag force depends on the relative velocity between the drops and the continuous phase. In a multiphase system, when the drag force balances the gravity and buoyancy forces, the resulting velocity is the relative velocity between the phases.
But most methods assume the resulting velocity is the terminal velocity of the dispersed phase in a stagnant fluid. A particular terminal velocity applies only to one particle diameter. By making the continuous phase velocity equal to the terminal velocity, all particles having that terminal velocity will not move or settle out. If particles and drops having only that particle diameter exist in the system, nothing gets separated until solid particles collide or liquid drops coalesce.
- At high dispersed phase hold-ups, dispersed phase settling becomes hindered and the terminal velocity is significantly reduced. Unlike hindered solid settling, as the dispersed phase hold-up increases, drop coalescence becomes more important. At some point coalescence starts affecting the drag force on the drop. Initially, at low coalescence rates, the terminal velocity decreases due to the hindering by other drops. As coalescence becomes more important, the terminal relative velocity starts to increase and dominates the hindering effect.
For solid particles, unless they stick together, no such coalescence occurs. The terminal velocity is then reduced and the solid particles become entrained in the continuous phase.
In the design of many systems, these effects are usually ignored. Either a conservative, effective, design particle diameter or a disengagement “K” value is used. The K-value method (reference 17) estimates the required continuous phase velocity to be used for design.
The design particle diameter and / or K-value is based on past experience. Although providing a workable design, the use of these methods can be very conservative, or they can provide for an unworkable design.
What if a design value for a particular system is not known? Guidance on design values are available only for a relatively small number of industrially significant systems. If a system deviates from these “norms”, then the dispersed phase hold-up, and the real particle diameter to be disengaged, needs to be known. A rough estimate of the dispersed phase hold-up can be made by assuming a homogeneous flow regime similar to vapor/liquid, two-phase pipe flow system analysis. The hold-up is then just the fraction of the total volume that is the dispersed phase.
However, if significant slip between the phases occurs, the homogeneous hold-up may not be correct. Relatively small changes in the dispersed phase hold-up can result in large changes in the dispersed phase settling velocity with ramifications for vessel sizes. For example, past experience (Reference 4) on a liquid/liquid system showed the ratio of dispersed phase velocity to that of a single particle to be about 0.7 at a dispersed phase hold-up of only 0.05 and about 0.5 at a hold-up of only 0.1.
If the homogeneous hold-up is greater than about 0.03, then experimental measurement of the actual hold-up needs to be considered.
The determination of solid particle diameters is relatively easy compared to that of liquid drops. Liquid drop diameters are difficult to estimate since they depend on the upstream process history of the fluid entering a vessel. It is well known that drop size within a system is inversely proportional to the energy dissipated per unit mass in that system. Therefore, upstream equipment with high energy input (agitators, pumps, etc.) or with high energy losses (high pressure drop control valves, pipe frictional losses, etc.) will tend to produce drops with small diameters. Various correlations are available to estimate drop sizes but they should be used with caution. Further information on drop size estimates can be found in References 5, 6, 7, and 8. Agreement by the client for the drop size estimated and to be used for vessel design is imperative. Note that this must be a true diameter and not an effective design diameter.
Once particle hold-up and diameter are known, the terminal velocity for a single particle in a stagnant media can be corrected to account for the presence of multiparticles. A number of methods are available:
- Ishii and Zuber (reference 9) developed drag coefficient and relative motion correlations from simple similarity criteria and a mixture viscosity model. They showed that the drag law for dispersed two-phase flows of bubbles, drops and particles could be put on a general and unified basis. Their unified method also accounts for the distortion of bubbles and drops.
- A Richardson / Zaki type of correlation as presented by Maude & Whitmore is described in references 3 and 10.
- The Zenz correlation for particulate fluidization (reference 11) can be used to directly estimate the relative velocity. The use of Zenz’s correlation to adequately determine the relative velocity in a counterflow, spray tower extractor is described in an older edition of Perry’s (reference 12). Note that much of the data Zenz used for his correlation was based on sedimentation data.
- The continuous phase superficial velocity can be estimated for vertical liquid/liquid separators directly from the extractor flooding correlation of Minard and Johnson (reference 13). The design velocity can be chosen at about 40 percent of the flood velocity.
- Rietema discusses other correlations in his review article (reference 14). This article is also an excellent discussion of dispersed two-phase systems.
None of these methods have been evaluated or compared. They are offered as starting references. Applicability to the particular system being analyzed should be determined.
As the dispersed phase hold-up approaches 0.2 to 0.3, drop coalescence effects may become important. Larger drops form due to the “crowding” caused by the high dispersed phase volume fraction. This author does not know of any current method for determining these coalescence effects. Reader suggestions are welcomed. However, a workable, conservative design can be obtained by neglecting coalescence and using a smaller particle size. For hold-ups of this magnitude, two separators may be required: one to knock-out the bulk of the dispersed phase and a secondary one for removal of the smaller particles.
Dispersion Bands
Liquid / liquid gravity separator performance depends on two phenomena:
- the movement of drops to the liquid / liquid interface;
- the coalescence of drops at the interface.
Liquid drops crossing the interface can form a deep band of dispersed drops (reference 7). Many design methods do not allocate vessel volume for a liquid dispersion band. They usually assume, for a liquid/liquid system, a dilute system and a conservative, effective drop diameter for design. This combination may provide enough volume for any dispersion band that may actually develop. But I have seen no data to confirm that. It is prudent to base the design on the actual, measured dispersed phase hold-up and the real, measured drop diameter. Adequate volume needs to be provided for a dispersion band. But if the band height is a significant fraction of the separator depth, a small increase in feed rate could flood the separator with the dispersion band resulting in poor, or no, liquid / liquid separation.
Davies (reference 5) presents a correlation for estimating the time required for coalescence of drops in a multi-drop system. Reference 7 provides some design criteria for determining the dispersion band volume.
Other Limitations
Other major assumptions are that the fluids are Newtonian and the drop sizes are above 2 mm. Perry’s (Reference 1) provides some guidance on non-Newtonian fluids. For small drops in a gas, the size can become comparable to the mean free path of the gas. Below about 2 mm in diameter, the terminal velocity of a drop in a gas needs to be corrected by applying the Stokes-Cunningham correction factor (see Zenz, Reference 11).
For particle sizes below 0.5 mm, Brownian motion becomes significant and can dominate gravity (see Reference 11). At these very small sizes, normal available disengagement calculation methods are not valid.
References
- Perry’s Chemical Engineers’ Handbook, 7th ed., P. 6-53.
- Handbook of Multiphase Systems, G. Hetsroni (ed), Section 1.3.9, “Hydrodynamics of Drops and Bubbles”, J.R.Grace, M.E.Weber, P.1-204, McGraw-Hill, NY, 1982.
- Handbook of Multiphase Sytems, G. Hetsroni (ed), Section 9.4, “Liquid-Liquid Separation”, R.A. Jaisinghani, McGraw-Hill, NY, 1982.
- Private Communication, Fluor Corporation, 3/2002.
- Handbook of Multiphase Sytems, G. Hetsroni (ed), Chapter 4, “Liquid-Liquid Systems”, J.C. Godfrey and C. Hanson McGraw-Hill, NY, 1982.
- Perry’s Chemical Engineers’ Handbook, 7th ed., P. 18-21.
- Handbook of Separation Process Technology, R.W. Rousseau (ed.), Chapter 3, “Phase Segregation”, L.J. Jacobs, Jr., W.R. Penney, P.148-156, Wiley & Sons, NY, 1987.
- Mixing in the Process Industries, 2nd ed., N. Harnby, M.F. Edwards, A.W. Nienow (eds.), Chapter 14, “Dynamics of Emulsification”, D.C. Peters, Butterworth-Heinemann, 1992.
- M. Ishii, N. Zuber, “Drag Coefficient and Relative Velocity in Bubbly, Droplet or Particulate Flows,” AIChE Jul, Vol 25, No. 2, p 843, 1979
- Perry’s Chemical Engineers’ Handbook, 7th ed., P. 6-52.
- Fluidization and Fluid Particle Systems, F.A. Zenz, D.F. Othmer, P. 236, Reinhold Publishing, NY, 1960.
- Perry’s Chemical Engineers’ Handbook, 4th ed., P. 21-24.
- Perry’s Chemical Engineers’ Handbook, 7th ed., P. 15-32.
- K. Rietema, “Science and Technology of Dispersed Two-Phase Systems-I and II”, Chemical Engineering Science, Vol. 37, No. 8, P.1125, 1982.
- The Handbook of Fluid Dynamics, R.W. Johnson (ed.), Chapter 18, “Multiphase Flow: Gas / Solid”, C. Zhu, L.S. Fan, CRC Press, NY, 1998.
- Flowing Gas-Solid Suspensions, R.G. Boothroyd, Chapter 2, Chapman & Hall Ltd, London, 1971.
- GPSA Engineering Databook, 11th ed., Vol. I, Chapter 7, 1998.