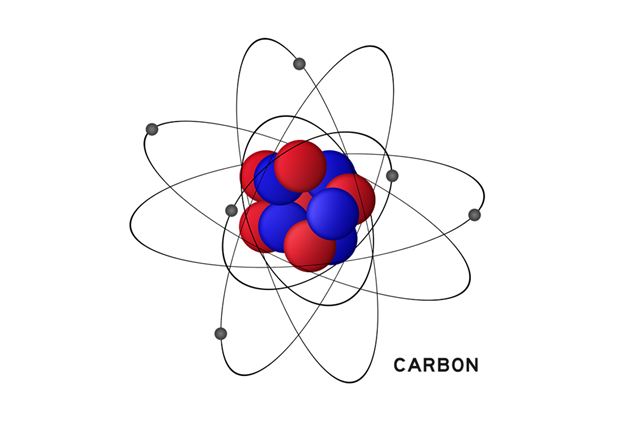
Adsorption on Activated Carbon – Part 2
Part 2 of this blog topic continues the discussion from last month of some important aspects of adsorption on activated carbon in the process industries and both parts are intended to serve as an introduction to the topic. The references cited at the end of this article are good starting points for further information.
Last month, in Part 1, we discussed some characteristics of activated carbon; the importance of understanding bed capacity; tradeoffs to be considered when choosing an adsorbent particle size; and fixed bed and carbon cannister units. This month, in Part 2, we will discuss the following:
- regeneration methods
- contaminant disposal
- some tips to keep in mind when designing a carbon adsorption system
Regeneration
Activated carbon which has reached its working capacity can be either regenerated for re-use or disposed and replaced with fresh carbon. Regeneration is the reversal of adsorption and is sometimes described as “desorption“.
Various processing methods are available and can be classified into the following general categories (References 1,3):
Temperature Swing Regeneration
For this method, desorption takes place at a temperature much higher than adsorption. The elevated temperature shifts the adsorption equilibrium resulting in contaminant desorption and regeneration of the adsorbent bed. To remove the thermally desorbed contaminant from the bed, a purge or sweep gas is utilized. A cooling step then returns the bed to its adsorption temperature.
Temperature swing regeneration is characterized by high capacities at low concentrations. This results in relatively long cycle times (hours to days). Most applications are for systems with low contaminant concentrations (purification).
Pressure Swing Regeneration
In this process, desorption occurs at a pressure much lower than adsorption. This pressure reduction shifts the adsorption equilibrium resulting in contaminant desorption and regeneration of the adsorbent bed. A purge step can also be utilized to increase contaminant recovery during this method of desorption. No heating or cooling steps are required for this method.
Most pressure swing regeneration cycles are characterized by low capacities at high concentrations. This requires that cycle times be short (seconds to minutes). Major uses for this process include purification and feed systems where contaminants are present at high concentration (bulk separations).
Inert Purge
Inert purging desorbs the adsorbate solely by partial pressure reduction. Many times this method is used in conjunction with the temperature swing and pressure swing methods. No heating or cooling steps are required for this method.
Like pressure swing regeneration, this method is characterized by low capacities at high concentrations with a resulting short cycle time. Bulk separations of contaminants not easily separable at high concentration and of weakly adsorbed components are especially suited to inert purging.
Displacement Purge
Regeneration can also be accomplished by using a purge fluid that is adsorbed at the cycle conditions. The purge fluid displaces the previously adsorbed contaminant. The contaminant is then swept away in the remaining purge fluid. A displacement purge can also be used in conjunction with the temperature swing and pressure swing methods
After displacement of the contaminant, some purge fluid remains in the adsorbent material. To remove the purged fluid during the next adsorption cycle, the contaminant in the feed must be more selectively adsorbed than the displacement purge fluid. But not all of the purge fluid may be removed. Therefore, a displacement purge can contaminate both the product stream and the recovered adsorbate. The displacement purge fluid must be carefully selected. A separation step (e.g., distillation) to purify the product during adsorption and another one to recover the purge fluid may be required.
In some displacement processes, steam is used to remove the displacement purge fluid. Sometimes a water wash can be used.
Disposal and Replacement
Disposing of spent catalyst and replacing it is one way of “regenerating” it. Disposal of spent activated carbon may be difficult in many cases since landfilling is no longer allowed in many countries in the world. Instead of regenerating in place, the carbon can be sent to a central regeneration facility and replaced with either fresh carbon or regenerated carbon
Particular processes for regenerating spent adsorbents include:
- Hot steam
- Hot gas (air, nitrogen, for example)
- Internal thermal heating of the bed
- Chemical and extraction methods
- Biological treatment
- Vacuum systems
- Electric and electrochemical methods
- Use of supercritical fluids
- Use of microwaves
- Ultrasound system
- Use of gamma-ray irradiation
- Photochemical treatment
After desorbing the adsorbed contaminant, the remainder of the regeneration cycle can include drying, cooling, or otherwise preparing the adsorbent to again adsorb. The regeneration step is the major consumer of energy in an adsorption process and does not depend on whether thermal energy or compression energy is used for regeneration (Reference 4). Methods to conserve energy are further discussed in Perry’s (Reference 4).
Contaminant Disposal
What one does with the desorbed material from the desorption step depends on the toxicity, flammability and permitting requirements for the compounds being disposed. It also depends whether or not the desorbed material can be easily and economically recovered. Costs for proper disposal of the desorbed gas or liquid can be significant and need to be considered when choosing a regeneration system. Also, spent carbon transport may require hazardous waste handling, adding additional costs.
There are three basic treatment options for the desorbed material:
Discharge to the atmosphere
For desorption using a hot gas, the desorbed gas, depending on its vapor concentration and permitting requirements, may be disposed of to the atmosphere.
Recovery
For large amounts of adsorbed solvent, or if the solvent is expensive, thermal desorption can be used for solvent recovery. Thermal desorption can also be used to recover any adsorbed residual product. Desorbed gases containing a dispersed solvent are immediately condensed or recuperated via membrane filtration. If steam is used for desorption, the recovered liquid will contain the solvent and water. The pure solvent can be recovered by decanting the water and then by distillation. The recovered material is then recycled to a storage tank or to the process. However, the water can be contaminated, and you may be left with a water emissions issue.
If the desorbed composition is complex, or the solvent or residual product quantities are too low, or the solvent cost is low, the solvents or residual product can be disposed by incineration. Burning the solvents directly in the gas phase, via after-burning, is also an option.
Incineration
For this option, steam may not be used to desorb but rather a hot gas may be used. When desorbing, the component to be removed is concentrated above the feed composition first entering the carbon bed adsorber such that the use of a combustion system for final destruction is facilitated. A common practice is to concentrate the recovered component to within 25% of its LEL. This method can be used to significantly reduce the amount of auxiliary fuel required in the combustion system. And it can facilitate economic design of recovery systems if the desorbed gas is captured by a membrane or recovered with a condenser. Commonly used combustion systems include flare, thermal oxidizer, incinerator, and furnace heater systems.
Safety, environmental and economic considerations all need to be considered when choosing a regeneration / disposal system. Important factors include:
- type of adsorbate – toxicity, flammability, corrosive nature, radioactivity
- types of adsorption – physical adsorption or chemisorption
- the costs of regeneration and disposal (contaminant and spent carbon)
Design Tips
- Keller and co-workers (Reference 1), have developed guidelines, in the form of a process selection matrix, that design engineers can use for choosing the most effective and economical regeneration process. Both gas phase and liquid phase systems are addressed. Perry’s (Reference 4) also discusses the use of these guidelines.
- Steam for regeneration should be superheated at a temperature higher than the boiling point of the adsorbate at regeneration pressure.
- Steam may be the most commonly used regenerant but there are situations where it should not be used. These situations should be identified and carefully evaluated. For example, steam used in a degreasing operation that emits halogenated Volatile Organic Carbons (VOCs) could cause the VOCs to decompose creating other issues.
- At the carbon surface, VOCs with a lower vapor pressure will tend to displace those with higher vapor pressure that have been previously adsorbed. Therefore, the bed’s capacity for the higher vapor pressure constituent decreases as the adsorption cycle proceeds. This needs to be considered when sizing the adsorber. A conservative design approach would base the adsorption cycle design on the least adsorbable component in a mixture and the desorption cycle on the most adsorbable component.
- In most processes, the contaminant feed composition and feed flowrate to the adsorption bed can vary significantly. But the system must always function to prevent contaminant breakthrough. Therefore, the design basis loading for the bed should be the maximum contaminant loading expected over the adsorption cycle — not the average loading over the cycle.
- Adsorber vessels are erected either in a vertical or a horizontal position. For horizontal vessels the carbon volume usually occupies no more than 1/3 of the vessel volume (Reference 9).
- Actual vendor quotes should be used for estimating capital costs. It is not likely that carbon cannister costs will inflate with the construction cost index or general inflation.
- A typical carbon bed has a useful lifetime of about five years. However, a lifetime as low as one to two years is likely if the adsorbed material is very difficult to desorb, polymerizes, or reacts with other constituents.
- If cannisters are likely to contain benzene they could be subject to the requirements in the Benzene Waste Operations NESHAP regulations. If so, disposal at landfills is not permitted and the carbon contaminated with benzene must be incinerated.
- Factors limiting the effectiveness of carbon beds include:
- Relative humidity greater than 50% can reduce carbon capacity.
- Elevated temperatures (greater than 38° C or 100° F) inhibit adsorption capacity.
- Biological growth on carbon or high particulate loadings can restrict flow through the bed.
- Some compounds can cause carbon bed fires because of their high heat release upon adsorption.
- Most adsorber systems are available as modular unit skids. When evaluating the pressure drop provided by a vendor for their unit, be sure the value provided is for the entire skid (inlet skid feed flange to outlet skid product flange) and not just for the carbon bed. Skid piping losses can be significant. Values for both the adsorption and desorption cycles should be obtained – they can be different. And for each cycle, start-of-cycle and end-of-cycle values should be provided.
- Adsorption testing of different activated carbons from several manufacturers may be necessary to determine the most cost-effective system. However, these tests should be performed with conditioned, regenerated carbon. That will provide a more realistic estimate of the adsorptive capacity during operation.
- An optimum adsorption cycle time exists. As the adsorption time cycle increases, the amount of adsorbent required increases. Therefore, the size, number, and cost of the adsorber vessels increase. Although shorter adsorption times require smaller adsorber systems with a lower capital cost, higher annual operating costs are required because the beds must be regenerated more frequently. In general, larger systems have better overall efficiency since less energy is used per pound of material adsorbed.
- Selection of materials of construction needs to consider potential partial decomposition of components during regeneration. For example, chlorinated hydrocarbons can decompose forming hydrochloric acid.
- During regeneration or adsorption, the temperatures should not be higher than the self-ignition point of the contaminant.
References
- R.W, Rousseau (ed.), “Handbook of Separation Process Technology”, Chapter 12 by G.E. Keller II, R.A. Anderson, C.M. Yon, “Adsorption”, Wiley & Sons, 1987.
- “EPA Air Pollution Control Cost Manual”, W. M. Vatavuk, W. L. Klotz, R. L. Stallings, EPA/452/B-02-001, Section 2/ Chapter 1 “Carbon Adsorbers”, 09/1999.
- CATC TECHNICAL BULLETIN, “CHOOSING AN ADSORPTION SYSTEM FOR VOC: CARBON, ZEOLITE, OR POLYMERS?”, EPA-456/F-99-004, May 1999.
- Perry’s Chemical Engineer’s Handbook, Section 16, Adsorption and Ion Exchange, 7th Edition, McGraw Hill, 1997.
- Wauquier, Jean-Pierre. (2000). Petroleum Refining, Volume 2 – Separation Processes. Editions Technip. A. Deschamps, S. Jullian Chapter 10: “Adsorption”; Chapter 11: “Adsorption in the Oil and Gas Industry”.
- Cheremisinoff, Nicholas P.. (2000). Handbook of Chemical Processing Equipment. Elsevier. Chapter 5.3: “Adsorption”.
- Albright, Lyle F.. (2009). Albright’s Chemical Engineering Handbook – Taylor & Francis. K.S. Knaebel, Chapter 14: “Adsorption”.
- DG 1110-1-2, DEPARTMENT OF THE ARMY, U.S. Army Corps of Engineers, Engineering and Design, “ADSORPTION DESIGN GUIDE” , 03/01/2001.
- EPA Air Pollution Control Cost Manual (7th Edition), J.L. Sorrels, A. Baynham, D. D. Randall, K. S. Schaffner, Section 3.1 / Chapter 1, “Carbon Adsorbers”, 10/2018.